A Clear View Ahead for Industrial Gear Units. DriveRadar® from SEW-Eurodrive
August 23, 2022
By Krystie Johnston
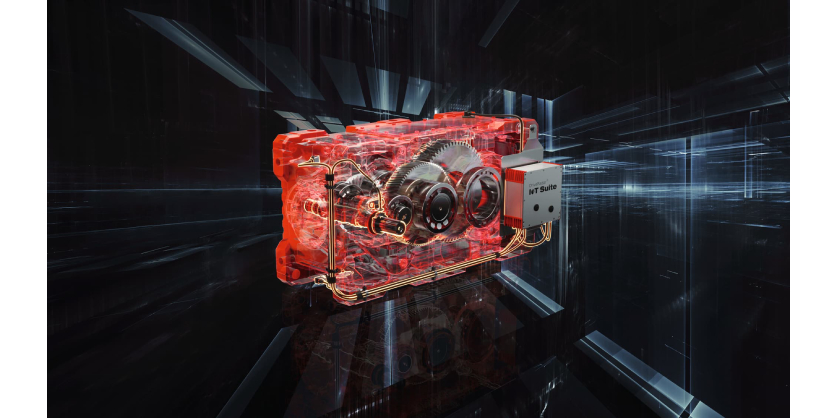
Editor’s note: Since publishing this article, SEW-Eurodrive’s DriveRadar has become available for their standard gear units in addition to their industrial gear units. See below for a link to their latest product development.
Industrial gear units are used in many production activities worldwide, particularly in the heavy industries such as construction, mining, oil and gas, and industrial machinery. These applications require significant mechanical work from the gear units and demand mechanical products that can get the work done reliably. These industrial applications are expensive to operate and insufficient equipment is not an option.
DriveRadar ® IoT Suite for industrial gear units
Considerable investments are made with respect to industrial gear units, and given this expense, it is reasonable that the owner or operator expects excellent system availability and improved productivity. It is not always possible to predict downtime and be able to prevent unscheduled maintenance. What if there was a way to get a clear view ahead, a way to achieve proactive maintenance and avoid costly breakdowns and even preventative maintenance? What if this solution was possible for not only new industrial gear units, but existing ones as well?
DriveRadar® from SEW-Eurodrive is that solution and more. This condition monitoring system records and assesses data from the gear unit to evaluate its current condition, provide forecasts to predict changes, and serves as a basis for predictive maintenance. Mechatronics Canada had the opportunity to sit down with Andy Chen, Product Manager – Large Industrial Gearing at SEW-Eurodrive and ask him about DriveRadar®. After a thorough question and answer and live demonstration, we bring to you an overview of DriveRadar®: condition-based component monitoring and maintenance forecasts for new and existing gear units.
The Demand for Condition Monitoring Is Increasing Tremendously
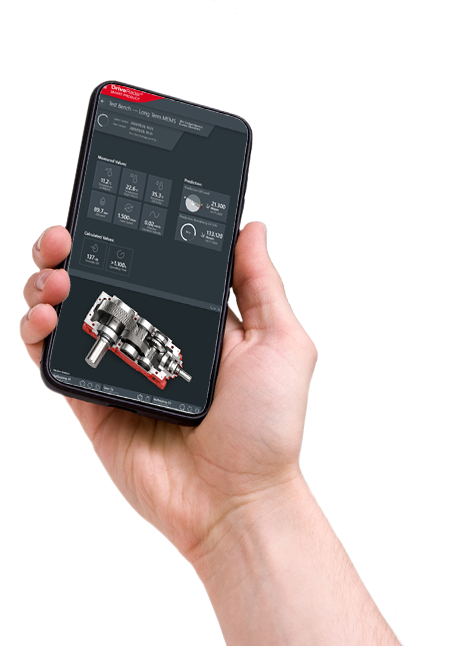
What is DriveRadar®?
DriveRadar® is a condition monitoring system developed by SEW-Eurodrive that can digitally record and automatically analyze gearbox data. The analysis results can be used to evaluate the current condition, as well as to predict the future state of the gearbox. As of today, DriveRadar® is available for the Industrial Gearboxes from SEW-Eurodrive, and consists of the following four elements: Sensors, Edge Processing Unit (EPU), SEW-Eurodrive Cloud, and a web-based human-interacting platform called “IoT Suite”. The full description of this system is “DriveRadar® IoT Suite for Industrial Gearboxes”. We will use the abbreviation “DRIG” in the rest of the article.
How does it work?
Sensors installed on the gear unit record physical variables that are relevant to the operation of the industrial gearboxes (vibration, oil level, oil temperature, ambient temperature, and input speed). The recorded data is then automatically evaluated and interpreted.
Continuous monitoring of the measured values ensures that the condition of the gearbox is transparent at all times. The underlying analysis procedures assign abnormalities directly to the affected components, display the trend progression, and allow critical conditions to be predicted.
“If a change in condition occurs, the user is informed immediately via email or smartphone App. Options for independent troubleshooting and the recommended SEW-Eurodrive services are displayed. With DRIG, maintenance can be planned in advance, and unexpected down-time can be avoided.”
Condition Monitoring and Maintenance Concepts
What is “condition monitoring” and “predictive maintenance,” and why are they important?
As it literally suggests, “Condition Monitoring” refers to monitoring the condition of an asset (in our case, an industrial gearbox). “Predictive maintenance”, on the other hand, is a maintenance strategy driven by predicting an asset’s condition. Compared to “Breakdown maintenance”, which refers to no maintenance until the asset breaks, or to “Preventative maintenance”, which refers to maintaining the asset on a regular basis regardless of its condition, “Predictive maintenance” is believed to be more cost-effective and less labor-intensive. “Condition monitoring” is a pre-requisite of “Predictive maintenance”.
Maintenance in industrial facilities is faced with continuously increasing demands. At the same time, the re-staffing of experienced personnel is difficult and cost intensive. The resulting loss of knowledge and cost pressure increases the need for automated, intelligent maintenance systems. Good maintenance ensures plant availability and thus reduces production downtime costs, and by extension, a company’s overall costs.
“New technologies can reduce maintenance costs. This makes it possible for companies to choose a cost-optimal maintenance strategy that results in a minimum total cost. Predictive maintenance is a lever for targeted cost optimization, and the prerequisite for this is condition monitoring of the relevant machinery and equipment.”
The more comprehensive and precise the functionality of the condition monitoring solution, the greater the relief for maintenance. Under preventative maintenance, day-to-day work involves much less on information gathering and on dealing with unexpected downtime.
The condition monitoring system indicates what needs to be done and when, and continuously adapts the necessary measures to the condition of the assets. With the system’s support, an on-site maintenance crew can concentrate fully on the actual activity and the resources required. Predictive maintenance actions are significantly supported by systems that offer forecasts to the user.
With condition monitoring, it is possible to prepare for upcoming events. The working method can then evolve from reactive maintenance to predictive maintenance.
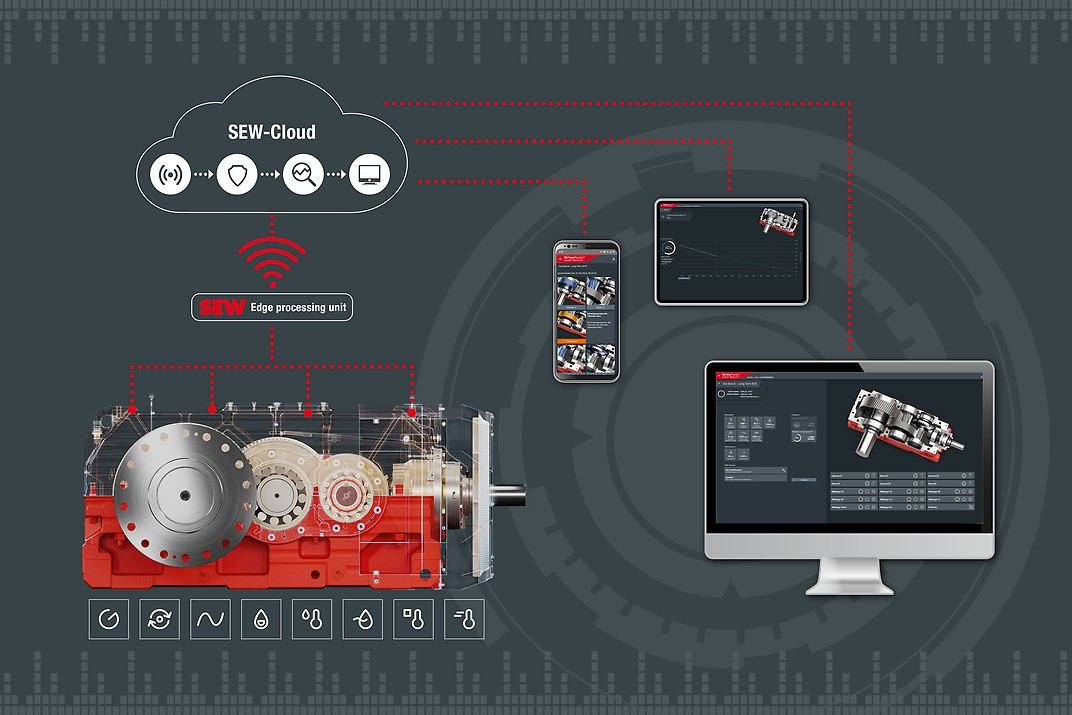
Functional elements of DriveRadar® IoT Suite for industrial gear unit
The Potential of Smart Maintenance
What are the benefits of using DriveRadar®? What, if any, are the drawbacks?
“The customer can monitor the gearboxes much more efficiently (and in many cases, more cost-effectively), since DriveRadar® makes all important gearbox characteristics transparent, comprehensible, and accessible. If a measured variable changes, the condition of the gearbox is automatically evaluated by the system and a warning is generated if necessary. This means that the customer can either check the digital platform (the IoT Suite) regularly or wait for the system to contact them when an anomaly occurs.”
The customer receives the notifications via the IoT Suite smartphone app or emails. Each notification contains a brief description of the warning and provides a recommended action. The customer can then take care of the anomaly in a timely manner, or contact SEW-Eurodrive directly from the web app for available services.
DriveRadar® does not impede any function of the monitored asset. It does consume electricity to keep the electronics operated, but the amount is insignificant compared to what will be required to run the industrial gearboxes. DriveRadar® requires little space, and can be installed either directly on the gearbox, or nearby. There is a cost associated with the hardware and the software. The former is one-time, and the latter is an on-going subscription.
Is DriveRadar® exclusive to SEW-Eurodrive’s products? What other manufacturer’s industrial gear units can it monitor? When will it become available for standard gear units?
DriveRadar® can be used to monitor other brands of gearboxes, as long as they are helical or bevel helical type. Currently, only the version for Industrial Gearboxes is available. In the near future, DriveRadar® will also be able to monitor the standard gear units.
DriveRadar® IoT Suite: The Web Application in Detail – Your New Maintenance Dashboard
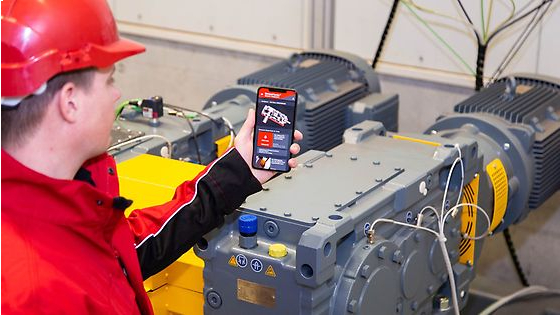
What is the “SEW-Eurodrive Cloud”? Where are the data stored, and is it secure?
The data is transferred directly from the industrial gearboxes to the SEW-Eurodrive Cloud via LTE. This means no intervention with the customer network. All the data are processed and interpreted at SEW-Eurodrive in an in-house ISO/IEC 27001 certified data center.
The data is transferred between the gear unit and the cloud via a secure connection using HTTPS. In addition to the measurement data, the transmission file contains a certificate for secure authentication and authorization of the hardware in the cloud. Thus, the channel is secured, and the identification of the hardware is also ensured.
The following are more details regarding IT security:
- SEW-Eurodrive operates a dedicated IoT certificate infrastructure in its own data centers.
- Encrypted communication between the EPU and SEW-Eurodrive Cloud according to TLS version 1.2.
- Identification of the edge devices via certificate-based SSL client authentication:
- The identity certificate as a “lifetime device credential” is designed for a long service life and uses ECC keys with 384-bit key length and SHA-384 signature.
- The short-lived operational certificates (for authentication during data transmission) use RSA keys with 2048-bit key length and SHA-256 signatures.
- Periodic renewal of operational certificates is done automatically using the EST protocol over an M2M mobile network.
What is the Edge Processing Unit (EPU), and how does it work?
An EPU is a micro-computer that is in close proximity to the points of data collection (sensors). It is connected to the sensors via cables, and its main function is to collect, refine, encrypt, and transmit the collected data to the SEW-Eurodrive Cloud for further analysis.
There are multiple benefits the EPU can offer:
- Higher data quality due to shorter cable length required for the sensors.
- Lower data usage due to refinement of the collected data before transmission.
- Better security due to data encryption before transmission.
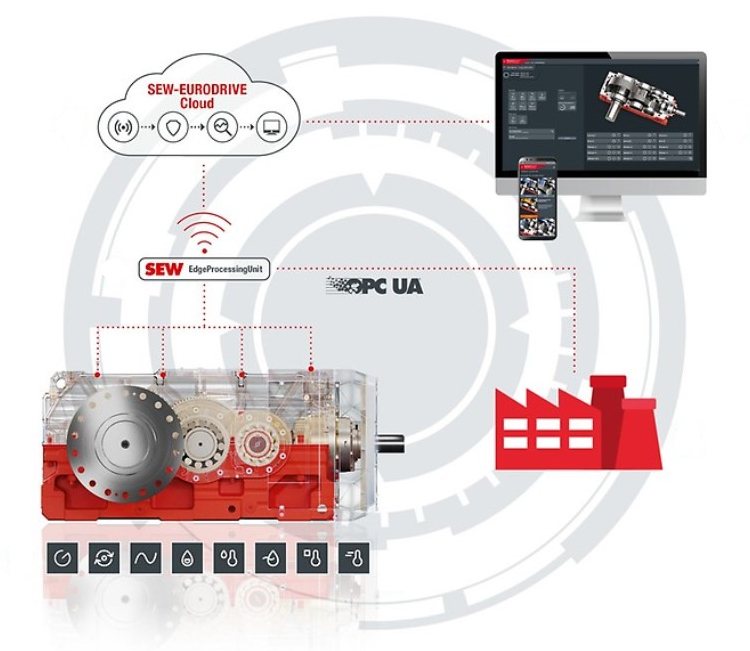
Direct data access for customers via OPC UA interface on the edge device
In addition, the implementation of the OPC UA interface in the EPU provides a flexible interface to the customer’s system on the field level. OPC UA (short for Open Platform Communications United Architecture) is a data exchange standard for industrial communication (machine-to-machine or PC-to-machine communication). The open interface standard has built-in security mechanisms and is independent of the programming language and the operating system of the application.
The OPC UA server provided on the EPU offers the possibility to integrate process data and status information of the industrial gear unit within the scope of the communication protocol. The only requirement for this purpose is that the OPC UA protocol is supported and an OPC UA client is provided in the customer’s system.
Your Added Value of a Comprehensive Solution
What kind of service and support does SEW-Eurodrive offer to customers of DriveRadar®? If they notice there is a failure, what are the recommended next steps?
Each warning message communicated to the customers will come with a recommended action from SEW-Eurodrive, which can be seen on the digital platform (IoT Suite). These actions include Expert Report, Endoscopy, Oil Analysis, Repair, Spare Parts Service and Retrofit. With a few clicks, customers can send a request to the corresponding SEW-Eurodrive local service rep and wait to be contacted within a reasonably short timeframe.
How does DriveRadar® improve the life of the industrial gearboxes?
“The operating variables DriveRadar® collects are vital signs of a gearbox’s overall health, and by continuously monitoring these variables and making predictions of their future trends, the gearbox’s lifespan can be improved.”
The following are some examples:
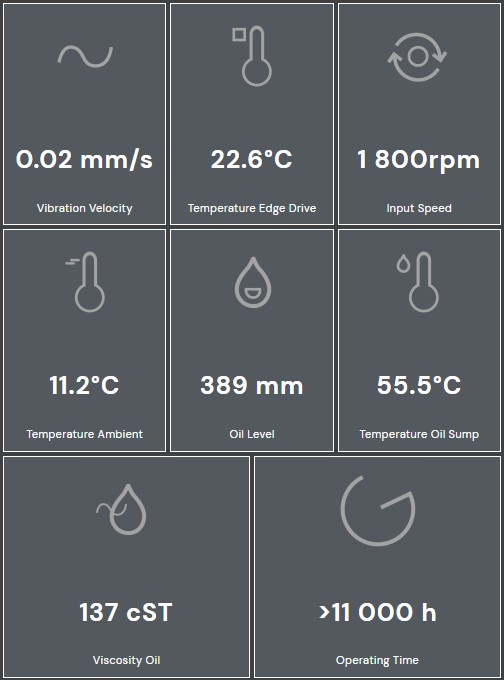
Vibration
Before any bearing or gearing fails, its vibration signal will start to deviate from normal value. This can take place days, weeks, or even months prior to the failure. By spotting this deviation at the early days, inspection and repair can be scheduled to prevent a large-scale failure of the gearbox.
Temperature
There are various causes that can contribute to an abnormal operating temperature of a gearbox, these include: wrong type or quantity of oil, contamination, misalignment, overload, change of environment, failing components…etc. By continuously monitoring the gearbox temperature, many of these causes can be identified and eliminated before they result in any permanent damage.
Oil Level
Too much and too little oil are both detrimental to the gearbox. That is why monitoring the oil level can contribute to long service life of the asset. This is especially true in the case where there is a gradual oil leak at a spot that is hard to be identified by the operator.
Over 3,000,000 measured values are acquired per day
With the collected data, DriveRadar® is also able to perform the following:
- Predict the remaining lives of the gearing and bearings.
- Predict the next oil change based on usage-dependent calculations of oil condition.
- Calculate the oil viscosity based on the recorded oil temperature and the type of oil used.
Andy, what is the take-away message you want customers to know about DriveRadar®?
DriveRadar® provides SEW’s customers with many valuable insights regarding drive technology. It supports the maintenance personnel in preventing unplanned downtime of critical assets, and can thus increase their contribution to the company’s success.
Thank you, Andy, for taking the time to discuss DriveRadar® with us and sharing your knowledge. Also, a big “thank you” to the rest of the very talented and dedicated team at SEW-Eurodrive who helped to facilitate this article.
More Information
Related Story
SEW-Eurodrive Showcases DriveRadar® IoT Suite
The DriveRadar® IoT suite package includes plug and play smart sensors, Edge processing, and intelligent data analysis to transform your static Gear units into sophisticated, self-learning, and self-diagnosing Gear Units.
The technology is designed to take the guesswork and even some of the thinking out of your maintenance tasks and allows you to view critical performance data right from your smart device.