Universal Robots Cobot Expo Series: Machine Tending North America
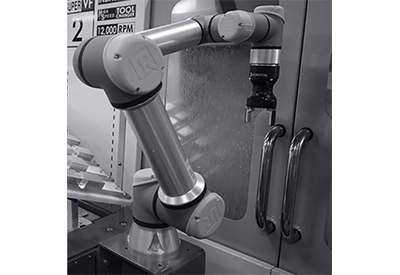
February 18, 2021
Date: February 23-24, 2021
The key to manufacturing success is keeping equipment running. Unfortunately, it can be hard to find and retain workers for tedious and potentially dangerous jobs such as machine tending. It’s not surprising that more than half of U.S. manufacturers are redesigning their workforce architecture around automation with machine tending as one of the most sought-after applications to automate.
But what tasks should you automate first? How do you make the cobot interface with the machine? Do you need a dedicated cell? Can you use the cobot on multiple machines? What about safety?
“Our Machine Tending Expo will help manufacturers address all these questions,” says Joe Campbell, Senior Manager of Applications Development at Universal Robots (UR). “Attendees at the Expo will be able to visit virtual booths featuring a wide range of turnkey solutions and application kits for easy deployment. In live demos and educational keynotes, they will learn all the ins and outs of machine tending with UR cobots.”
The Machine Tending Expo is free to attend with registration now open at: urrobots.com/machinetending
New robot tending systems on display
Universal Robots is building a rapidly expanding network of Certified System Integrators (CSIs); many CSIs offer not only help with UR cobot deployment but also develop turnkey robot tending systems to address parts presentation and robot-machine communication.
Alex Webster, owner of UR CSI SDMS Robotics, has helped machine shops of all kinds integrate UR cobots. “This is the essential technology that was needed to bring robots into widespread use for machine tending,” he says, calling Universal Robots “the most important step forward in machine shop automation since the advent of CNC, the pallet changer, and the bar feeder.” At the Expo, SDMS will introduce the SDMS Machine Tending System consisting of the UR10e cobot arm, SDMS’ robot interface system, and specially-designed robot mount.
Often, manufacturers just need help to get started, whereafter they can succeed with cobot automation by becoming autonomous and do DIY projects. That is the goal for UR CSI Revtech Systems, launching the new CNC Loader Revflex at the Expo. “We strive to share our knowledge with customers so they require us less and less throughout their other projects,” says Catherine Bernier, application engineer at Revtech Systems, who will present the keynote “How Robotics Done Right Can Change Your Business.”
Brian Knopp, general manager of UR CSI ProCobots, emphasizes that buying a standardized machine tending system eliminates the mystery and misery manufacturers face when trying to navigate a fragmented market of cobot products and accessories. “When someone wants a fishing boat, they go buy one. They don’t buy the motor and then build the boat themselves,” says the general manager of ProCobots, that will be showcasing the company’s practical CNC machine automation solutions with UR cobots.
When Universal Robots released the e-series line of cobots featuring repeatability down to 30 microns, Troy Ojalehto, owner of UR CSI Rapid Design Solutions, was excited. “When you’re doing multi-op precision machining, the accuracy requirements go way up,” he says. “Universal Robots’ repeatability really competes in the same space as traditional industrial robots but with all the safety and flexibility that cobots offer.” Rapid Design Solutions’ Expo booth will focus on how small to medium size machine shops can efficiently automate even low-run production with UR cobots without major process overhaul.
UR+ Application Kits reduce project risk and complexity
With the UR+ platform, Universal Robots launched the industry’s largest and most comprehensive ecosystem of products certified to integrate seamlessly with UR cobots. Several UR+ partners will exhibit new machine tending related UR+ products and Application Kits at the Expo, among them Robotiq that launched the CNC machine tending kit.
Adam Schmidt, Robotiq’s Director of Sales for Americas, will present the keynote “8 Key Learnings in CNC Machine Tending Cell Deployment From 13 Years of Experience.” The company’s Expo booth is a rich educational experience with both eLearning programs and demos featuring solutions and products Robotiq provides to simplify the design and programming of a CNC machine tending cell deployment.
Manufacturers visiting UR+ partner New Scale Robotics’ Expo booth will learn the benefits of enhanced machine tending with real-time part measurement. The company’s UR+ certified Q-Span Workstation Kits powered by UR3e cobots combines part handling, QC measurements, and data logging for small parts.
Cobots never staying idle and always monitored
Moving cobots between different machining cells presents a whole new set of programming and logistical complexities that can be overwhelming at first. UR+ partner Flexxbotics’ mission is to free robots from being fixed in place. At the Expo, Flexxbotics will show attendees how the Flexx Connect product platform provides localization and communication tools to redeploy UR cobots on multiple jobs and stations, driving up the utilization rate of the robot while reducing the time needed to achieve a positive ROI.
Remotely monitoring the cobot is another key to machine uptime. In the live demo “Do you know what your cobot is doing right now? Get your cobot to tell you in less than 10 minutes,” UR OEM partner Hirebotics will show how using the company’s software platform Beacon allows manufacturers full monitoring capabilities by cloud-connecting their cobots through a smartphone app to maximize productivity. Through Beacon, manufacturers get real-time access to program variables, IO, and log files while receiving alerts if production is down.
“The innovation happening right now within cobot-powered machine tending operations is phenomenal. We look forward to sharing these solutions with Expo attendees soon,” says Universal Robots’ Joe Campbell.