How Omron, MICHauto and Square One Education are Helping Students Bridge the Gap Between STEM Education and Careers in Manufacturing
May 2, 2023
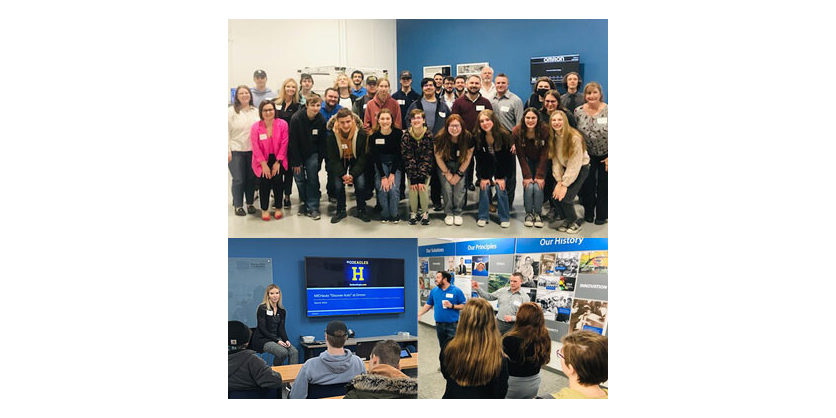
How Omron, MICHauto and Square One Education are helping students bridge the gap between STEM education and careers in manufacturing. Most recent high school and college graduates can attest there’s a bit of a skills gap between what they learned and what they’re expected to do in their first job after graduation. In some industries, this gap can be immense, and it can create4 stress for the new hires even when employer-provided training is thorough.
The automotive industry falls into this category, but companies, universities, and outreach organizations are working to change that. With STEM education programs that connect students to today’s major automotive manufacturers and suppliers along with generous donations from companies like Omron that put cutting-edge equipment directly into classrooms, today’s young people are more prepared.
Hartland High School students visit Omron’s Detroit Proof of Concept Center
As part of its talent attraction efforts, MICHauto (Michigan’s only automotive, mobility, and technology cluster association) has partnered with Square One Education Network to identify and engage high school students within the Detroit Region and the state. Through in-person and virtual career exploration of automotive and mobility companies and presentations by industry experts, Discover Auto tours educate students on the industry, its technology, and promote diverse career options. Hartland High School attended the first in-person tour since 2020, which took place at Omron’s Detroit Proof of Concept Center (PoCC) in Novi, Michigan.
Our PoCC engineers gave the students a demonstration of the latest automotive-focused automation technologies, including autonomous mobile robots (AMRs). Omron sales and marketing colleagues also discussed what it’s like to work in the industry and shared tips on navigating the educational pathways to STEM careers in engineering and manufacturing.
What automotive companies are looking for in the workforce
Trends like rapid technological development, concerns about sustainability, and the advent of electric vehicles are influencing how automotive companies hire their next generation of workers. As the vehicles themselves become increasingly complex, companies are looking for highly flexible employees who can easily adapt to new automotive manufacturing solutions.
Automation promises to continue revolutionizing the automotive factory floor, and employees will be required to learn how to work alongside — and in some cases, directly with — technologies such as collaborative robots, mobile robots, and the like. When young people gain familiarity with these technologies before their first day on the job, this becomes much easier.
Are you a recent college graduate interested in gaining a foothold in an automation career, including within the automotive industry?
Sakura Early Career Training Program
Related Story
Omron’s Robotic Solutions: Thousands of Possibilities
Robots can improve the productivity of many industries and processes. They can handle a variety of tasks, such as laborious or repetitive work, and can dramatically improve processes in industries such as machine tending, assembly, packaging, and other manufacturing activities. Moreover, they can handle routine operations, allowing employees to perform higher-value tasks.
This article will look at a selection of Omron’s robots and robotic solutions, such as autonomous robots and collaborative robots, and will explore how these products can be integrated into facilities to improve productivity. It also discusses the next evolution in factory automation: MoMa’s, or Mobile Manipulators – the growing trend of having collaborative robots mounted onto AMRs to achieve new levels of automation.