Endress+Hauser Customer Experience Centre Wins Rethinking The Future Award 2022
December 12, 2022
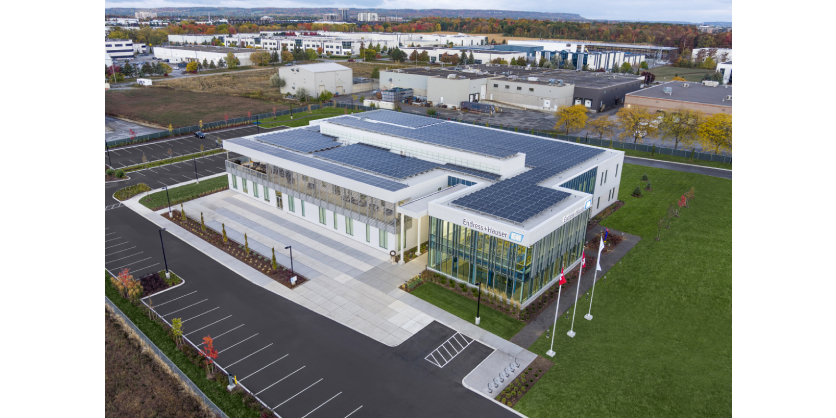
The Endress+Hauser Customer Experience Centre named winner of the Rethinking The Future Award 2022 in the Industrial (Built) category.
Rethinking The Future award is an annual architecture award program which aims to promote outstanding work in the field of architecture and design across the world. Over 1000+ registrations were received from more than 40 countries, spanning architecture, landscaping, urban design, product design, and interior design in ~50 categories.
The new 47,000 sq. ft. Customer Experience Centre for the Swiss-owned corporation establishes a new sustainability standard for its international portfolio of buildings. The project built within an industrial park in Burlington, Ontario, is the first privately owned project in Canada to pursue both ZCB Certification and LEED Gold simultaneously. It recently achieved ZCB Certification, the first of two sustainability milestones.
The Customer Experience Centre is home to a wide variety of spatial typologies including workplace and administrative zones, the Process Training Unit (PTU), multipurpose training rooms, workshop/repair area, Factory Acceptance Testing (FAT) and calibration labs, kitchen and cafeteria areas, fitness room, and warehouse space.
The client team was well-versed in advanced technologies and excited to see how far we could push sustainability outcomes for this diverse space. Led by data, the outcome is a high-performance building enclosure, creative mechanical system solutions, sustainable materials selection, supported by sustainable construction practices. We can anticipate the site will produce more energy than the facility will require on an annual basis.
Project Team:
- Architecture: mcCallumSather
- Mechanical Engineering: mcCallumSather
- LEED/Net Zero Facilitation: mcCallumSather
- Structural Engineering: WSP
- Electrical Engineering: WSP
- Energy Consultants: RWDI
- Civil: MTE Consultants Inc.
- Landscape: GSP
- Solar Energy: Zon Engineering Inc.
- Geothermal: Geo-Xergy Systems
- Noise Engineer: Novus Environmental (now part of SLR)
- Construction Management: G.S. Wark Limited
- Photography Credits: Philip Castleton
The project built within an industrial park in Burlington, Ontario, is the first privately owned project in Canada to pursue both ZCB Certification and LEED Gold simultaneously. It recently achieved ZCB Certification, the first of two sustainability milestones.
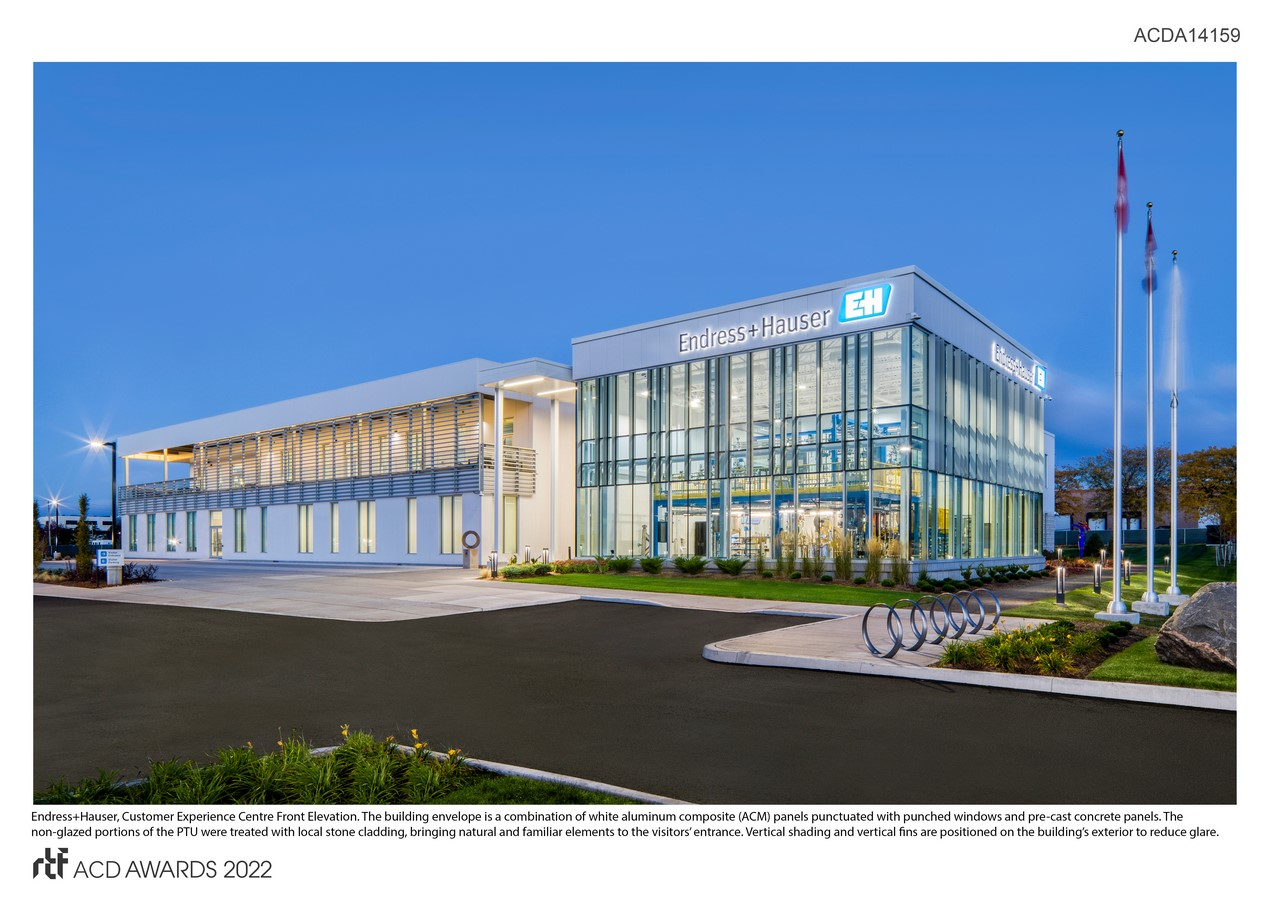
Endress+Hauser, family owned and run, sees each new building as a gift for its employees. The Customer Experience Centre is home to a wide variety of spatial typologies including workplace and administrative zones, the process training unit (PTU), multipurpose training rooms, workshops/repair areas, calibration process rooms, kitchen and cafeteria areas, fitness room, and warehouse space. It all supports sales, training, and repairs of its measurement instrumentation, services, and solutions for industrial process engineering. Our design prioritized natural daylighting, indoor air quality and creating opportunities for movement within and around the building.
The glass enclosed process training unit (PTU) is prominently positioned at the southeast corner, acting as the building’s public face, immediately an educational opportunity for visitors and connected visually to two of its boardroom areas, including one which cantilevers out into the PTU space for a bird’s eye view of the PTU in action.
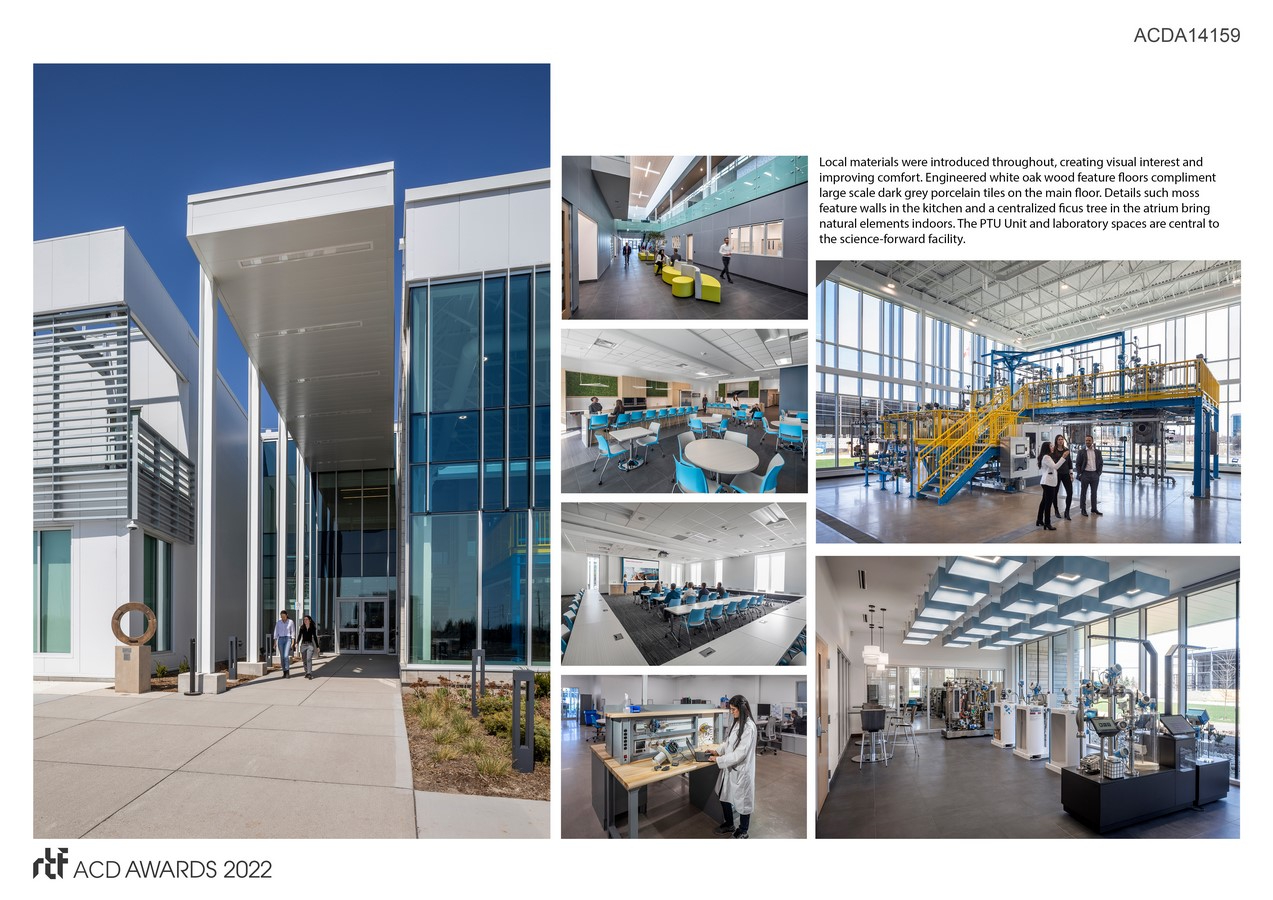
The atrium and corridor area visually connects with the calibration and specialized laboratory zones on one side and training, entertainment, and cafeteria zones on the other. It gave the Endress+Hauser team much more flexibility to host guests, employees and customers at events of various size and scale.
For the workplace areas, we spent time with its employees to gain a thorough understanding of the company’s culture and workflow. As a result, the open concept second floor houses employee working areas grouped into neighbourhoods, with slight shifts in layout to accommodate differing work types. A combination of open flexible work areas, breakout rooms and enclosed offices are organized around a central walking track within the triple height atrium, creating openness. To counter this openness, we paid special attention to the acoustics, facilitating employee comfort and focused work.
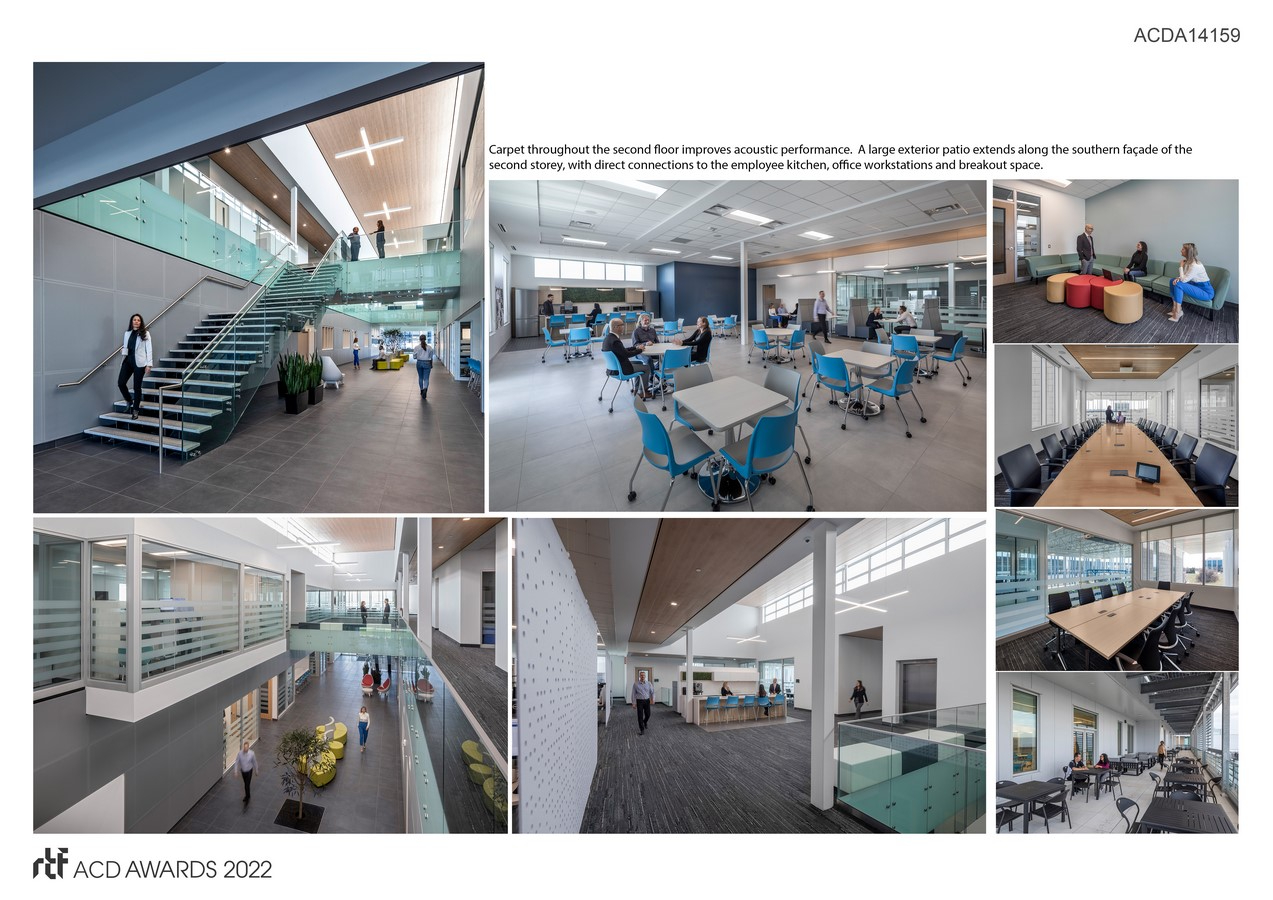
An important design objective was to provide access to the outdoors. A large exterior patio extends along the southern façade of the second storey, with direct connections to the employee kitchen. Additionally, over 40% of the formerly vacant property has been dedicated to open space and landscaping. These areas have been planted with native, non-invasive and drought tolerant plant species that absorb and hold rainfall to reduce the amount of surface water runoff. A walking trail encircles the sites, a place for respite for its staff or the location of walking meetings.
The client team was well-versed in advanced technologies and excited to see how far we could push sustainability outcomes. Data informed our team’s decisions. The outcome is a high-performance building enclosure, creative mechanical system solutions, sustainable materials selection, supported by sustainable construction practices. The data tells us we can anticipate the site will produce more energy than the facility will require on an annual basis.
Related Story
Endress+Hauser’s New Customer Experience Centre
The Customer Experience Centre. Four thousand four hundred square meters of sensationally detailed architecture, designed to ensure a superior customer and employee experience. The CEC showcases Endress+Hauser’s best-in-class instrumentation. It has a full-service calibration laboratory capable of handling the entire spectrum of flow, temperature, pressure, and level instrumentation – unmatched by any in the country.