Comau Leverages Advanced Automation To Deliver Faster Time-To-Market And Enhanced Flexibility For The New Alfa Romeo Tonale
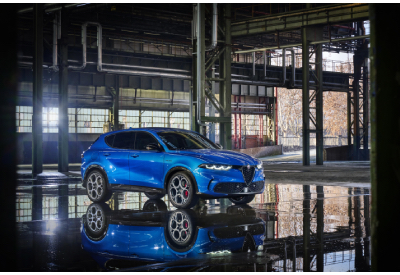
November 23, 2022
Comau Leverages Advanced Automation To Deliver Faster Time-To-Market And Enhanced Flexibility For The New Alfa Romeo Tonale
- •Comau has built, retooled and deployed 20 state-of-the-art manufacturing lines to produce the Body-in-White of Alfa Romeo’s all new Tonale
- •The expanded framework can handle multiple versions of the SUV (hybrid and traditional engine architectures) in random mix
- •The system is flexible enough to simultaneously produce both the SUV and a significantly smaller compact vehicle
- •The complete solution is based on the companies’ commitment to steadfast quality and features 468 Comau robots, advanced assembly processes, laser welding, plasma cutting and vision systems
- •The quality guaranteed by Comau’s processes and production equipment fully addresses the stringent requirements of a premium brand like Alfa Romeo
Comau has designed and deployed a flexible Body-In-White (BIW) manufacturing solution for the all-new Tonale, the first Alfa SUV of the new generation, meeting both the customer’s rigorous production targets, quality goals and time to market objectives.
The new and enhanced 20 lines are designed to allow the automaker to assemble its mid-size Tonale in a random mix of up to 4 different versions while maintaining the desired throughput. Fully scalable, the innovative solution lets the automaker produce multiple brands on the same line while allowing them to further expand production in the future if and when it is needed. Moreover, Comau’s ability to execute the entire project to deliver maximum quality in terms of processes and production equipment, has allowed the joint project team to ensure the value of the final product while fully meeting the stringent requirements of a premium brand such as Alfa Romeo.
Tasked both with building five completely new lines and retooling 15 existing lines to accommodate the new Tonale, Comau deployed the production lines in record time despite multiple challenges. The SUV chassis is significantly larger than the compact car for which the line was originally designed, and Comau was asked to make the necessary changes without sacrificing production of either vehicle. Through simultaneous engineering, the team designed a transformation strategy that allowed Comau to execute the retooling operation in parallel with the existing activities, according to its “Zero Loss Launch” philosophy. Comau also worked on the lines during the plant’s natural downtime, thus minimizing any impact on production.
As part of Comau’s lean manufacturing approach, the automated and semi-automated production solution is based on the proprietary ComauFlex technology, nicknamed Butterfly due to its impressive agility and use of suspended robots. This set-up allows Alfa Romeo to change or modify a specific vehicle model by adjusting the robot tooling, not the arrangement of the robots themselves. In addition to protecting the scalability of the customer’s initial investment, the solution is designed to enable the introduction of new models in the future for a fraction of the initial expenditure. Indeed, the entire system features 468 welding robots, 148 of which are completely new and 320 taken from existing lines. Comau utilized advanced simulation tools during the entire development period, guaranteeing the best quality product and throughput.
In addition to allowing Alfa Romeo to perform the complex bodyshop processes with extreme precision, the Comau-designed solution fully assembles the entire BIW from start to finish. With the aid of three different vision systems to aid the automated picking and positioning of pieces, the robots weld, fasten and perform other activities, including the spreading the semi-structural adhesive on the parts and plasma cutting during the end-of-line activities. All said, the process involves the insertion of roughly 2,800 welding spots for each model.
With significant net output, Alfa Romeo can bank on substantial savings in terms of time, long-term costs and production efficiencies. Moreover, because the solution is a fully modular system built around standard products that are combined within an expandable design framework, the automaker can quickly expand its manufacturing environment with limited impact on existing production.
“To join forces with a prestigious brand such as Alfa Romeo is an incredible opportunity to develop cutting edge technologies and we are proud to see the tangible results of Comau’s field-proven expertise within the collaboration between two Italian examples of excellence,” explained Pietro Gorlier, Comau CEO. “Our commitment to unwavering quality is seen within the processes and products used to make the Tonale, and allow us to ensure maximum value for the customer.”
“In supporting the Alfa Romeo brand in their product expansion, Comau has fully leveraged its longstanding experience in automation and smart manufacturing to deliver an unprecedented level of flexibility,” added Andrew Lloyd, Comau Chief of Engineering. “This innovative approach to implementing brand new technologies and retooling existing lines and equipment is a direct result of our commitment to offer increasingly scalable and sustainable solutions, helping our customers better meet their objectives today as well as tomorrow.”