ABB Survey Reveals Unplanned Downtime Costs $125,000 Per Hour
Global survey commissioned by ABB underscores the close relationship between uptime and reliability, emphasizing the importance of effective maintenance strategies and service partnerships
October 13, 2023
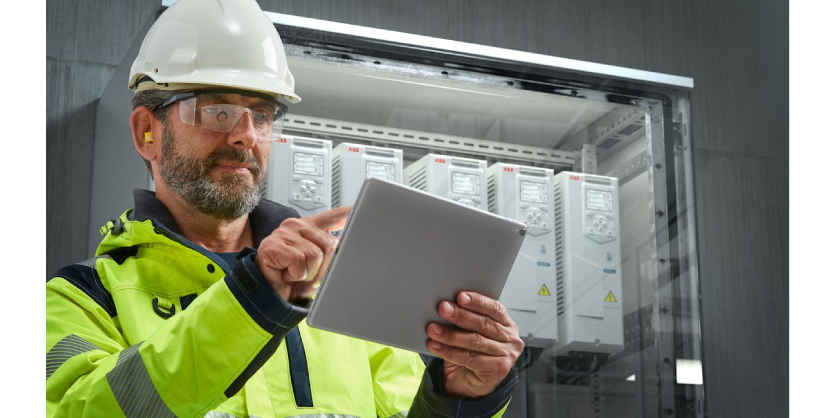
• Global survey commissioned by ABB underscores the close relationship between uptime and reliability, emphasizing the importance of effective maintenance strategies and service partnerships
• An outage lasting for an eight-hour working shift would cost one million dollars
• 87 percent of respondents are interested in how outcome-based maintenance agreements can boost business success
According to the new “Value of Reliability” survey from ABB, over two-thirds of industrial businesses experience unplanned outages at least once a month, costing the typical business* close to $125,000 per hour**. Despite this, 21 percent of businesses surveyed still rely on run-to-fail maintenance.
The survey, conducted by Sapio Research in July 2023, gathered responses from 3,215 plant maintenance decision-makers globally across the energy generation, plastics and rubber, oil and gas, wind, chemicals, rail, utilities, marine, food and beverage, water and wastewater, and metals sectors. It is part of a report that provides insights into how businesses currently manage maintenance and how they can reduce unplanned downtime.
The findings demonstrate the importance of equipment reliability and maintenance. Ninety-two percent reported that maintenance has increased their uptime in the last year, with 38 percent reporting an improvement of at least a quarter. Also, three-quarters of respondents said that reliability positively impacts their business reputation and financial performance, and helps them meet contractual obligations, prevent waste and secure repeat business. Reliability was rated by respondents as the top priority when purchasing new equipment.
Looking forward, 60 percent plan to increase their investment in reliability and maintenance in the next three years, with a third planning to boost spend by more than 10 percent. Nine in ten respondents expressed interest in outcome-based maintenance agreements. Under these, operators pay service partners based on achieved outcomes, such as increased uptime or energy efficiency. This results in efficient and effective service delivery with predictable cashflow.
Speaking about the results of the survey, Virve Viitanen, Head of Global Customer Care and Support at ABB’s Motion Services division, said: “There’s no typical length for an outage, but consider one that lasts a working day of eight hours – based on the median hourly rate, it would cost a business one million dollars. With this in mind, industrial businesses should aim to progress from a high-risk run-to-fail maintenance approach to a long-term outcome-based strategy. This will improve reliability, business reputation, competitivity, cut costs, and provide peace of mind – empowering businesses to focus on their core competence.”
Virve Viitanen, Head of Global Customer Care and Support at ABB’s Motion Services division
This new, outcome-based model to maintenance will help industrial businesses meet incoming emissions targets and regulations as the world fights against climate change. In addition, it will help overcome the industry skills gap as experienced technicians reach retirement age.
For more information, read the full survey report.
*Notes to editors: the median value was used rather than the mean/average. Because of the distribution of answers, the median is a closer representation of the typical organization.
**The survey is based on information provided by third parties in response to a questionnaire, rather than reviewing actual accounting records.
ABB (ABBN: SIX Swiss Ex) is a technology leader in electrification and automation, enabling a more sustainable and resource-efficient future. The company’s solutions connect engineering know-how and software to optimize how things are manufactured, moved, powered and operated. Building on more than 130 years of excellence, ABB’s ~105,000 employees are committed to driving innovations that accelerate industrial transformation. www.abb.com
ABB Motion keeps the world turning – while saving energy every day. We innovate and push the boundaries of technology to enable the low-carbon future for customers, industries and societies. With our digitally enabled drives, motors and services our customers and partners achieve better performance, safety and reliability. We offer a combination of domain expertise and technology to deliver the optimum drive and motor solution for a wide range of applications in all industrial segments. Through our global presence we are always close to serve our customers. Building on more than 130 years of cumulative experience in electric powertrains, we learn and improve every day. go.abb/motion
Related Story
The Future Is Digital: How Industry Is Moving Towards Sustainability
While climate change is top of mind for everyone, industry plays a critical role. As the biggest consumer of natural resources and the largest source of greenhouse gas (GHG) emissions, industry faces a major challenge. How can we lower emissions and reduce resource consumption while delivering more productivity and profitability—on a short timeline, given the state of the planet? In recent years, an increasingly popular approach in industry has been digitalization.