Four Trends in Bottling and Capping Machinery
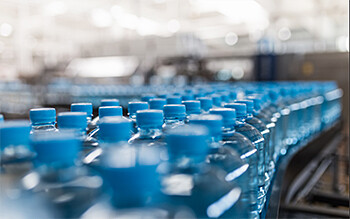
Aug 6, 2021
Despite the economic disruption caused by the COVID-19 pandemic, the demand for packaged products – and a greater variety of such products – is continuing to rise. Specifically, manufacturers in the beverage industry are faced with the pressure of providing the requisite product diversity while ensuring compliance with new FSMA standards.
Let’s take a look at four ways in which bottling and capping machine builders are dealing with these challenges.
1. Seeking better equipment that speeds up the changeover process.
When the number of SKUs is growing, it’s more crucial than ever to keep the changeover process short and sweet. When companies struggle to find processes that efficiently accommodate changeovers, these changeovers take even longer than usual due to the fine-tuning required.
For this reason, many manufacturers are looking to invest in machines that require little to no fine-tuning post-changeover. By minimizing complexity and utilizing machines with centerlines that are simple to understand, manufacturers can improve their systems’ performance even when new challenges arise.
2. Investing in modular technologies that enhance flexibility.
Flexible manufacturing is essential for companies that produce many different products in varying combinations. Beverage packaging companies need equipment that can dynamically switch between container and cap sizes and apply the correct labels to various items. A go-to solution for this need is to use a collaborative robot.
Collaborative robots can be easily “taught” new tasks or variations on tasks involving slightly different shapes or sizes. Guided by machine vision, these extremely flexible robots can recognize different product types and determine the appropriate next step. When combined with a mobile base, a collaborative robot can offer a fully modular material handling solution.
3. Implementing more robust systems to ensure FSMA compliance.
The Food Modernization and Safety Act (FSMA) was put in place to prevent foodborne illnesses through greater manufacturing and supply chain oversight. To ensure the proper hygienic conditions outlined in these standards, manufacturers must perform washdowns regularly. This necessitates technologies that can withstand harsh chemicals and water pressure.
One of the requirements of FSMA is that manufacturers must identify the immediate supplier and the immediate recipient (aside from the consumer in a retail situation), so that a product can be traced throughout the supply chain. This is prompting a greater investment in robust traceability systems to ensure compliance.
4. Building complete liquid filling and capping solutions from a single automation supplier.
Incorporating technologies from multiple suppliers into a single bottling or capping machine can lead to slower performance and more complex troubleshooting. Many end users are now seeking to buy complete packaging lines with multiple functions from a single source. Omron is one of the few automation partners capable of providing an end-to-end solution.