Creative Motion Control: High Speed Linear Actuators
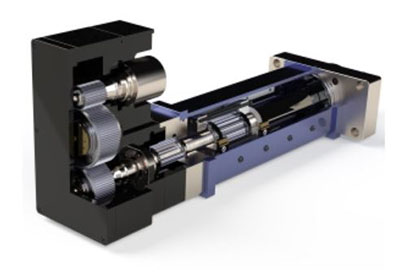
June 3, 2021
What Is an Ultra High Speed Linear Actuator?
An actuator is a component in a device that makes a particular kind of motion happen. Actuators are usually part of a larger system that includes sensors, structural components, and elements that interact with the world in a particular way.
Different types of actuators produce different types of motion. A linear actuator produces motion in a straight line and is appropriate for use when transferring various kinds of energy, such as rotational energy, into linear motion.
Electric elevators and motorized wheelchair lifts use linear motion, so they rely on linear actuators. A typical car jack is an example of a mechanical linear actuator. It converts the rotational motion provided by the user into energy that moves a vehicle up or down. High speed linear actuators are typically used when lighter loads need to be moved at higher speeds.
The P-15 ultra high speed linear actuators can achieve speeds as high as 9 inches per second, making it suitable for applications that require rapid movements such as sorting and movements of a robotic arm.
Important Features of a High Speed Heavy Duty Linear Actuator
An actuator must have a mechanism to obtain energy. For example, a car jack’s lever connects to a gear that transfers energy to the lifting element. In electric linear actuators, an electrical motor typically rotates a gear. For actuators driven by gears, the gear size and thread width influence the function.
Consider the gears on a bicycle or in a car’s transmission.
A linear actuator must have a component that is capable of moving in a straight line, from side to side, or up and down.
High speed linear actuator must typically be mounted securely to a stable structure so that the actuator itself remains fixed in place while in operation. In some cases, like with a car jack, the weight of the actuator keeps it stable. However, for precision control, mounting and other stabilization processes might be necessary.
Applications of a Linear Actuator (High Speed)
Recent trends toward automation and the development of the Internet of Things (IoT) have allowed the digital world to have a direct physical impact. Automated factories, robot surgery, autonomous vehicles, and several other systems operate under computer or computer-assisted control. Software must be able to move real-world objects precisely and rapidly to accomplish many tasks. Here are just a few examples of practical applications of high speed linear actuator technology.
- ● NASA’s rovers depend on actuators for precise control of sensors and instruments for analyzing mars, asteroids, and other locations in space.
- ● In robot and remote surgery, linear actuators generate precise movements of surgical instruments.
- ● The United States Postal Service uses linear actuators for high-speed automated sorting of mail.
The Power Source of a High Speed Linear Actuator (12V)
Actuators are often powered by electricity but can be powered by other energy sources, such as steam or compressed gas. Piezoelectric actuators generate linear motion by using specialized materials that produce mechanical energy (in other words, they push) in response to an electrical current.
The P-15 High Speed Linear Actuator uses a 12V power source so that it can run on a conventional U.S. power outlet, eliminating the need for adaptors, transformers, or alternative sources of power.
Generation and Transmission of Rotational Energy in a High Speed 12 Volt Linear Actuator
Linear actuators can convey rotational energy in different ways. For example, gears and belts can transmit rotational energy. Gear-driven actuators are called rack-and-pinion actuators, with pinion being another word for gear.
The P-15 High Speed Linear Actuator uses a 12 volt DC motor that imparts energy to a steel alloy gear, which generates rotational energy that must be converted into linear motion. The motor has a 20% duty cycle, meaning it can be on up to four minutes within a twenty-minute time frame.
Conversion of Rotational Energy to Linear Energy in a High Speed 12 Volt Linear Actuator
For a linear actuator to function, it must effectively generate linear motion of some component from the rotational movement of the belt or gear. In the rack-and-pinion actuator, a gear (the pinion) contacts a linear structure with cogs called the rack. As the gear turns, it slides the rack sideways.
A lead screw linear actuator consists of a threaded screw and a nut that encircles the screw. As the nut rotates, the screw moves relative to the nut and anything attached to it. In some actuators, the nut moves sideways, and the screw is fixed. In others, the nut is fixed, and the screw moves.
In roller screw actuators, rollers are placed between the screw and the nut surfaces to reduce friction. In ball screw actuators, ball bearings are placed in grooves between the screw and the nut to produce the same effect.
In the PA-15, the linear motion is achieved by the motion of a screw, like in the previous examples.
Mounting of High Speed High Force Linear Actuators
There are two common ways to mount an actuator: stationary mounting and dual-pivot mounting.
Stationary mounting is particularly suitable for situations where allowing the actuator housing to move exposes it to vibration or makes precise control difficult. If the actuator is moving delicate equipment or controlling precision movements, stationary mounting could improve performance and extend the life of the equipment.
Dual-pivot mounting connects each end of the actuator with a pin or other connector and allows the actuator to swivel. This gives the actuator freedom to move while remaining attached to the power source. Clevis mounts and trunnions are common mounts for dual-pivot mounting. If you need to pivot along more than one axis, a spherical mount is an appropriate choice.
Many factors must be considered when choosing a mounting style, such as speed, type of rotation, the nature of the equipment being used, the need for stability, and other factors. It is critical to be aware of the stresses that motion could place on the actuator and other components. The mount should allow motion in desired directions while preventing unwanted movement and vibration.
The PA-15 is mounted using BRK-15 mounting brackets that are compatible with dual-pivot mounting.
Control of High Speed Linear Actuators
Linear actuators can be “smart” technology. They can be connected to the internet for remote operation or controlled by a computer system. The actuator could be controlled by a human operator, a remote-control device, a Wi-Fi signal, or an internal computer. Automation and autonomous control of devices is a developing field. New advances in machine learning, neural networks, and other forms of digital technology enable increasingly sophisticated autonomous control.
The P-15 High Speed Linear Actuator is designed to work with control boxes that easily plug into the actuator for computer control. Creative Motion Control staff can help to find a control box to suit each customer’s needs.
Customization of High Speed Linear Actuators
Depending on the application, high speed linear actuators can have additional features. High Speed Linear actuators like the PA-15 are durable. However, some applications exceed the limits of what most linear actuators are designed for. High speed linear actuators can be customized to be waterproof, shielded from radiation, or capable of working in other extreme environments.
- ● A lock can prevent the actuator from moving in one or both directions.
- ● A stop block prevents the actuator from moving beyond a certain range.
- ● Feedback from a motion sensor could allow for adaptive control of the actuator that takes into account its own motion. For example, an actuator with a motion sensor could use the positional feedback to stabilize an instrument moved by the wind or an impact. It could also send an error signal if the actuator is stuck.