White Paper: Robots – There’s One for Every Job – How to Choose the Right One
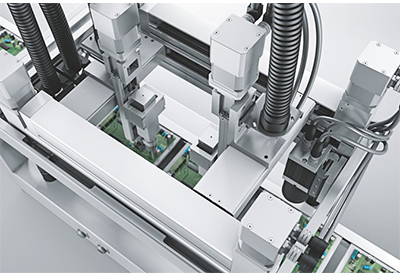
March 18, 2021
By Kevin Tardif, Business Development Specialist – Electric Automation, Festo
This white paper provides information on:
- – Automation 0: History of robotics
- – Different types of robot technologies
- – Benefits and limitations of each technology
- – Factors to consider in selecting the right robot for the job
Executive summary
In the popular imagination, robots are large, dumb machines for doing dull, muscular, repetitive tasks with precision and accuracy. That’s only part of today’s robotics world. Robots now come in many sizes and configurations, with two to seven axes. They can do simple or complicated work, even surgery. For both factory and process automation, there’s one to suit just about any application or budget – anywhere productivity can be enhanced by automating the movement of tooling or payloads, or performing production tasks better or faster. Payloads can be anything from computer chips weighing a gram to locomotive wheelsets weighing over a ton.
There is a vast assortment of end-of-arm tooling to perform simple or complex tasks, from grippers to multi-tool end-effectors. Robots are easier than ever to integrate into any manufacturing or processing environment, including food zones, clean rooms and warehouses. All that said, given this plethora of options, it’s more important than ever to know which type of robot best fits a company’s needs from both a capabilities and cost standpoint. The major types of robots – articulated, cartesian, SCARA, delta and cobot – each has strengths and limitations. Understanding these plusses and minusses is a necessary starting point for making an initial investment in robotics.
1. Robotics: A half century of evolution
For a half century now, robots have been the centerpiece of Industry 3.0, which is typically defined as the age of pre-digital automation. They will be just as critical if not more so as the world transitions to Industry 4.0, the digital automation age. Robots have been changing the industrial landscape since their introduction in the 1970s; they represented a quantum leap in productivity, flexibility and reliability. Almost any repetitive motion involving the movement of an object – be it tooling like a welding gun or sheet metal being welded – can be done faster and with greater precision and repeatability by a robot.
Early on, the image of the large, six-axis articulated robot welding car and truck bodies became fixed in the popular imagination. Articulated robots have spread throughout and beyond heavy industry with many improvements to the robot itself as well as the development of more end effectors – end of arm tooling – to address the wider need for flexible automation. Articulated robots are used in sectors as diverse as healthcare, food and beverage, steelmaking, warehousing – wherever there are repetitive or environmentally or ergonomically challenging tasks that can be accomplished faster, more reliably and/or more cost-effectively. Robots are even assembling new robots.
New concepts in robotics
Initially, this robot revolution provided major manufacturers like automakers with even greater economies of scale, but offered nothing to most small- and medium-sized businesses. More recent developments in cartesian robotics (linear), SCARA and delta robots to name the most widely used as well the newest commercial innovation, collaborative robots – have made automation accessible to businesses of almost any size. (This whitepaper focuses on electrically powered robots, but pneumatics are now being integrated into robots to actuate specific tasks. The BionicCobot is a project of the Bionic Learning Network which consists of a team that investigates what the production of the future can learn from nature.)
Each type of robot comes with benefits and limitations. For would-be new adopters of
robotics, it’s important to understand those possibilities and pitfalls.
Robots come with 1-7 axes, each axis providing a degree of freedom. A two-axis cartesian gantry typically plots on the X-Y or Y-Z axes. A three-axis robot has three degrees of freedom and performs its functions through the X-Y-Z axes. These small robots are rigid in form, and cannot tilt or rotate themselves, although they can have attached tooling that can swivel or rotate or adapt to the shape of a small payload. Four- and five-axis robots have additional flexibility to rotate and tilt. A six-axis articulated robot has six degrees of freedom – the flexibility to move objects in any directions or rotate them in any orientation. The latter type is generally chosen when an application requires complex manipulation of objects. The seventh axis allows extended reach in one axis; in other words, it allows displacement of the six-axis articulated robots.
Seven-axis robots are likewise fully free; the seventh axis can allow additional orientations to manoeuvre tooling in tight spaces. For example, such a robot can weld a car body frame from the inside of the cabin by inserting the end effector through the window opening and rotating it backwards 180 degrees. Seven-axis robots can operate up closer to the work piece than other articulated robots for potential space savings.
2. Articulated robots: benefits and limitations
The popularity of six- and seven-axis articulated robots reflects the great flexibility that six degrees of freedom permit. They are easy to program, come with their own controller, and movement sequences and I/O activation can be programmed via a user-friendly teach pendant. In most applications, only a basic knowledge of programming is required to activate the robot. On the hardware side, industrial articulated robots can be relatively small or massive (capable of handling loads like locomotive wheelsets weighing over a ton). They can have substantial reach, over three meters with certain models. This range of sizes makes articulated robots suitable for a great number of industries and applications involving making or moving of materials or finished goods.
The articulated robot also has issues which can restrict its utility or boost its cost profile. A small-sized articulated robot is easy to install; its base only need be bolted to a frame or floor. But it can only lift so much or reach so far. Where the job requires a larger robot, civil engineering may be required to ensure the structure can handle the weight and torque caused by the load offset. An articulated robot grows in reach and payload simultaneously. The longer the reach, the greater the payload it can manage, the more space and engineering it requires, the more it costs. Where an application involves handling a small load over a long reach or a heavy load over short distances, an articulated robot may not be the most cost-effective solution.
By design, the articulated robot occupies space and footprint that can’t be utilized for other purposes. It also has singularities, i.e. locations and orientations in the surrounding space it cannot access. These spatial limitations require more complex safety precautions since the robot will often be used in zones where workers are present, even just occasionally. Expensive devices, such as zone scanners or safety mats are often necessary, and more advanced functionalities are then required, such as Safely-Limited Speed (SLS), or Safe Speed Monitor (SSM). The fact it requires its own controller to handle the inverse kinematics (the conversion of the multiple motor rotary positions to usable cartesian coordinates and orientation in space) can also represent a double dip from a hardware perspective, since in certain cases the robot controller will need to communicate with a higher-level PLC on the production line. The bottom line is an issue as well. Where the full flexibility of a six-axis robot is not required, like many pick-and-place or packaging applications, other types of robots may do the job just as well if not better, and at a lower cost.
3. Cartesian robots – benefits and limitations
One of those lower-cost alternatives is the cartesian or linear robot. Its design consists of an assembly of linear actuators and sometimes a rotary actuator at the end of arm for 3D applications. It’s easy to install and maintain. The cartesian robot is fully adaptable; strokes and sizes of each axis can be customized to the application. Its reach and payload are independent of each other, not intertwined. The linear axis comes in a number of designs which further adapt it to the function it performs. For example, toothed belt actuators allow high velocities while ball screw actuators permit high precision and high feed force, with pick rates up to 100/min fairly typical of this type.
The adaptability of these handling systems makes them price-optimized for a wide range of straightforward applications where the dexterity of an articulated robot isn’t required. That can involve extremely light to very heavy parts placement, sorting or box-loading, device inspection and much more. Another major advantage and differentiator of the cartesian robot is its excellent space economy. It allows full access to the footprint it occupies. There is no dead space or singularities. Safety requirements are less stringent and hence less costly since the robot’s reach is limited to its small working zone. Fences, door switches or light curtains are often sufficient to ensure proper safety. Little space around the robot is wasted.
Programming the cartesian robot doesn’t usually require a specific motion controller. Since the actuators are moving along the workspace coordinate system axis, interpolation of the motors position is not mandatory to determine the robot end-of-arm position in space. In other words, no calculation of inverse kinematics is needed. The system PLC can often be used to control each axis directly, without the addition of a second controller. Also, cartesian robot designs are readily scalable, and are more often than not composed entirely of standard, catalog components from servo drives/motors and controller to slides and grippers. That’s part of their affordability and assures replacement parts are readily available and quickly installed.
The cartesian robot’s main limitation is comparative inflexibility. It will easily accommodate linear movement in three axes, and a forth, rotative axis. However, one has to add a motion controller to perform more complex synchronized tasks, such as CNC. Cartesian robots are rarely used in washdown environments; they don’t provide sufficient protection against water ingress. Precision and thoroughness at installation is required. Each axis must be carefully aligned, and surface flatness must be adequate, especially in larger systems. Cartesian robots are also configured uniquely for each application. While product or packaging format changes can be performed quickly via the PLC, mechanical modifications of the unit may be required for more extensive changes in the application. Finally, cartesian robots, if used without a separate motion controller, may require more programming time than other robot types. Teach pendants are less common, so programming of sequences must be done in the PLC, with each axis addressed and commissioned individually.
4. SCARA robots – benefits and limitations
SCARA robots have been designed and optimized for light applications. (The SCARA acronym stands for Selective Compliance Articulated Robot Arm, although some use Assembly in place of Articulated.) They are a streamlined version of articulated robots. Their simplicity and small size make it easy to integrate on assembly lines and they can achieve quite impressive cycle times, with high accuracy. They are very adept at functions like inserting components in spaces with tight tolerances while maintaining their rigidity in such movements, which makes them a cost-effective choice in a lot of pick-and-place applications as well as small parts handling. (In performing such tasks, there are accessories like feeding systems to maintain a constant supply of parts.) Programming and commissioning is relatively easy and fast, using the manufacturer- supplied teach pendant.
But with low cost come limitations. The SCARA robot requires a dedicated robot controller and is limited to planar applications. It is generally restricted to three axes. It may be the optimal solution where its full capability – three or four degrees of freedom – can be used, but if the job only requires two (horizontal and vertical movement, for example), the SCARA robot cannot be reduced to a two-axis system, making it less attractive than a cartesian gantry-style robot from both the cost and performance standpoint. Like the articulated robot, the SCARA robot footprint also extends further than the working zone, resulting in a loss of functional space in and around the unit.
5. Delta robots – benefits and limitations
The delta robot is mainly renowned for its speed, with pick rates up to 300/min. Its mounting type puts it above its working zone, limiting the loss of footprint. It is often paired with a vision system to pick pieces randomly placed in more complex sorting and packing applications. Just like the articulated and SCARA robot, it will generally be provided with a teach pendant for easy programming.
On the other hand, the delta robot’s payload capacity is generally much lower than alternative technologies. Its wirey inverse tripod design makes it less robust than the other robot options, which reduces its maximum payload weight. That performance limitation is the price for achieving such a high dynamic capability. The delta robot has a quite limited working envelope. Its design does not allow long reaches. Like cartesian and SCARA robots, delta robots are generally limited to four axes and cannot provide the flexibility of an articulated robot. Its complex assembly makes it more difficult to maintain and repair. And if used as a top mount on a large machine, there may be a need to reinforce the machine frame to bear the added weight.
6. Collaborative robots – benefits and limitations
Collaborative robots, or cobots, are a relatively recent development with a promising future in making possible safe human-machine interaction. By allowing a direct collaboration between a worker and robot, they are adding a dimension to our understanding of how automation can be integrated into industry. A cobot can be an articulated, cartesian, SCARA or Delta robot, although to date, most would be categorized as articulated. They come with payload capacity of 4-35 kg, scaling up in size and reach (also price) accordingly. There are models with up to seven axes; the latter can perform tasks that are particularly challengingly ergonomically, and are even being used as independent production line robots. The difference between cobots and other robots is their built-in safety features that allow direct interaction with humans, without protective shielding, safety curtains or other safety features. Since they don’t need fixed external safety barriers, some cobots can be mounted on mobile platforms to go wherever they are needed. It is important to note that a safety evaluation of the application has to be done, and while the cobot itself might be safe, if the tool being used on its end of arm is sharp, an external safety barrier likely would be needed.
Cobots are limited in speed and payload, which disappoints some users looking for a conventional robot that doesn’t require expensive safety protection. The greatest value of cobots is where they can free a skilled employee from the menial aspects of their job to concentrate exclusively on the high value aspects. For example, in complex device assembly requiring a deft human touch, a cobot can perform simple handling or manufacturing tasks in support of the worker, who can then focus exclusively on the part of the job that makes full use of their skills or knowledge. It’s a valid approach, providing the productivity boost provided by the collaboration delivers a reasonably quick payback of the investment. Otherwise, it can turn into what amounts to an expensive vanity project.
7. Considerations in making your choice:
Understanding the application
In approaching an investment in robotics, one should consider all aspects of an application prior to making a final selection. Here are some factors to consider:
*Reach and payload
The reach and payload should be the first criteria, as it may immediately shorten the list of suitable options. On technical grounds alone, a large heavy load would rule out any consideration of lightweight handling technologies. On the other hand, if the reach is long but the payload weight is low, a lower cost cartesian robot might suffice.
*Flexibility
If an application requires five or six degrees of freedom, an articulated robot may be the only viable solution. If it is, one option for the price sensitive business requiring one or two robots might be repurposed (used) units. However, for simpler applications, like small parts positioning and loading, electronic parts insertion, and box and machine tool loading – any application where two or three axes are sufficient – why pay for more axes than the application calls for?
*Speed
Does the application require a high pick rate, like that of a delta robot (up to 300/min is fairly common), or would a lesser pick rate of cartesian gantry or SCARA robot suffice? Here’s a real world example: A machine builder constructed two virtually identical custom box loading/palletizing machines for a dairy to load yoghurt containers into boxes. Each machine was intended for a different container format. For the first machine boxing plastic tubs, a high pick rate was required, so a top mounted delta robot was installed for maximum throughput. For the second machine boxing four-packs (2×2) of single serve cups, a lower pick rate was sufficient, and the machine builder was able to reduce the cost to the end user by substituting a two-axis cartesian gantry as the box loader.
*Space and footprint
More and more, machine and production line footprints are key planning concerns. Floor space is expensive, and companies want to optimize their shop floor layout. Cartesian and delta robots provide a clear advantage over the other technologies, since only vertical space is lost, which is generally less critical.
*Engineering and project development
Design, assembly, installation and commissioning time and expense should be factored into comparative costing, especially incorporating a robot into a larger machine or system. Delays in receiving and assembling the robot could hold up the entire project. There are online and software tools that can minimize engineering and procurement risks. Festo, for example, created the Handling Guide Online, where an engineer can design an application-specific cartesian handling system like a 2D or 3D gantry in 10 minutes or less by entering just a few data points, receive the price and CAD document for it immediately at no cost, and in most cases have the finished product delivered pre- assembled and pre-tested in an average of three to four weeks.
*Maintainability, repairability and availability
Unscheduled downtime is every production manager’s nightmare. Robots should be relatively easy to maintain and repair. This is a particularly important issue for businesses which don’t have a large robotic fleet with in-house technical know-how. Who is going to fix the robot? How long will it take? What is the lead time for delivery of critical replacement parts like motors and controllers? During planning stages, these issues are often overlooked at one’s future peril.
*Standardization – when good is good enough
Standardization within a company or industry could be a valid consideration on business grounds, even if the robot selected is not the most ideally adapted or even the cheapest but capable of doing the job. Sometimes, the well-travelled path will prove to be the one of least resistance (and risk).
8. Conclusions
The proliferation of robot technologies has enabled businesses of all sizes to access the benefits of automation. Which one’s “best”? It’s usually the one that is the “best fit” – not just for achieving the productivity gains from the investment and satisfying the technical requirements of the application, but also from the standpoint of related issues like plant safety, space utilization, and of course, the going-in cost and after-sales support.