Smart Pneumatics Role in Automation, Cobots, Safety and System Efficiency
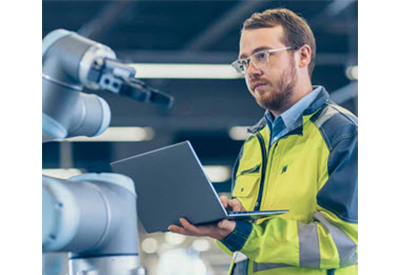
January 14, 2021
By Herman Wang, director, global business development, In-Plant Factory Automation and Linda Caron, global product manager for Factory Automation, Pneumatic Division
For today’s industrial pneumatic systems, automation and efficiency continue to be the driving factors in design. Automation in pneumatics incorporates a variety of design strategies and considerations. When it comes to industrial machinery, Industry 4.0 and the Industrial Internet of Things (IIoT) are big buzzwords, but these solutions are not fully developed yet. For design engineers working toward creating closed-loop automated systems, questions for consideration include:
-
How do you develop the next-generation Smart Factory?
-
What is the path toward a fully automated factory?
-
How can maintenance requirements be triggered without any downtime?
-
What data input can you use and how do you capture that data?
-
How do you diagnose maintenance issues at the component, system, or process level?
Smart connected pneumatics
For design engineers, smart pneumatics can mean complete flexibility; this is the ability of that component to communicate over the network, multiple uses for a single device, ease of integration and commissioning, as well as troubleshooting. Smart products are where you see the most difference in pneumatic systems. The diagnostic aspect of smart pneumatics is important to help achieve zero downtime.
The concept of zero downtime has seemed unrealistic in the past, however, technology is evolving in that direction. Incorporating sensors into pneumatics enables end-users to collect important prognostic and diagnostic data for setting alerts and getting machine feedback.
The future of smart pneumatics is a complete plug-and-play configuration that is easy to manage. For today’s smart pneumatics, design engineers can generate data and set the alerts but are not yet making fully closed-loop systems. However, this is on the horizon with end-to-end systems that can be configured with just a few clicks and the device will be able to take over, provide data and feedback into the control system that goes beyond simply allowing data dumps.
Read our white paper Innovations for Automation and Efficiency in Industrial Pneumatic Systems and gain insight into the use of smart pneumatics, designing for cobotic applications, applying safety standards, and pneumatic system efficiency.
Technology is changing–quickly
As technology evolves, seemingly almost daily, more people are migrating to networks as designers are migrating systems to the newer industrial Ethernet systems. Why? Overall, the “line” topology of the networks makes them much easier to work on and troubleshoot.
It used to be the case that each manufacturer offered the same type of components such as cylinders and FRLs. There is a large divide in the market on what is available and what functions they offer. Products today with integrated electronics offer many different functions through what is embedded. When specifying systems, design engineers should be sure to understand what is necessary for the machine and what value can be provided by the smart products that are specified.
Cobots and safety
In automotive manufacturing, robotics has been in use for more than a decade and over the years, they have shifted from being hydraulically driven to being pneumatically driven. In industrial cobot applications, collaborative robots, known as “cobots” work with humans in some way, including as an assistant or guide in a task or process. Unlike autonomous robots, cobots, do not work alone. They are designed to work with human instruction or respond to human behavior. The shift to pneumatics for robotics means that cobots are primarily pneumatically driven.
Cobots are the next big thing in industrial applications as the cost of robotics comes down and newer opportunities are being developed. Leading cobot applications include:
-
Machine tending where cobots can load and unload tools and accessories to decrease manual handling.
-
Pick and place where cobots can complete careful packing and moving, then place and position products or parts.
-
Assembly and flexible manufacturing where cobots insert parts, screwdriver, and other assembly tasks with appropriate end-of-arm tools.
-
Packaging, loading, and unloading when aided by suction or gripper attachments, cobots move finished products through packaging.
Safety in collaboration of manual and automated
The strict separation between the manual work of the factory worker and the automated actions of robots is becoming an increasingly gray area. Their work ranges are overlapping and merging into a collaborative working space. In doing so, humans and machines will be able to simultaneously work together on the same workpiece or component in the future—without having to be shielded from each other for safety reasons.
Due to this, safety is the largest consideration in the design of cobot applications. However, there can be some confusion on which safety standards to follow in applications with cobots due to the divide between traditional pneumatics and entering the world of robotics. As standards and their adoption vary among engineers and facilities, it is important to know which standards to apply.
For incorporating cobots into a plant, engineers must understand the required standards for the facility and compile the necessary documentation and technical file with due diligence, testing, and validation of the controls architecture.
Smart pneumatic system efficiency
Lower upfront and maintenance costs combine to make pneumatics the most popular and cost-effective choice for executing mechanical motion. New improvements in designs and efficiency of compressors, and the standard use and distribution of clean dry air in a manufacturing facility, also make pneumatics a good choice for industrial automated machinery. Smart pneumatics aim to help generate and maximize data and minimize compressed air use. Compressed air use by industrial machines is a close second to the use of electricity in terms of cost, and well ahead of other utilities such as water and natural gas in most plants and facilities. Electricity is less expensive per dollar of unit energy, but compressed air and pneumatics have many other advantages encouraging their use.
Effective pneumatic systems need properly sized, installed, and maintained components from compressors to workstations. A few wrong choices can lead to everything from wasted energy to system failures. Conversely, even seemingly small design tweaks can add up to large improvements in pneumatic system efficiency. These changes can save air, reduce costs, improve overall utilization, and reduce downtime in operation.