Three Ways to Deal With No-Reads Caused by Low-Contrast Barcodes
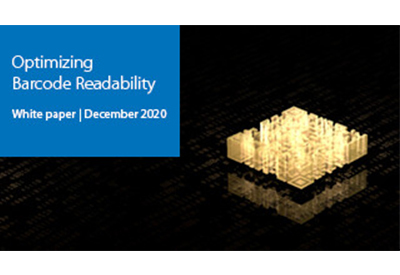
December 24, 2020
To extract data from a barcode, a reader must be able to differentiate between the symbol’s light and dark elements. If there’s insufficient contrast between them, the reader may be unable to distinguish the barcode from its substrate. This would cause a no-read, which in turn could result in wasted time and unnecessary amounts of scrapped product.
Contrast problems can be caused by multiple underlying issues, including lack of consistency in the production of light and dark elements across the code, the amount of variation or noise in the background or substrate, or lighting conditions that create reflections or shadows on the substrate. These uniformity issues can make a barcode reader blind to the symbol.
Let’s take a look at some possible ways to troubleshoot this category of barcoding problem.
1. Adjust the printer to ensure consistent application of ink.
Ensuring distinct and uniform barcode elements is the first step to preventing unreadable codes due to low contrast. If printing or marking method is causing inconsistencies, it’s important to adjust the printer or marking equipment to ensure that ink is applied evenly across the whole symbol or that the marking equipment is abrading the substrate with uniform pressure.
2. Adjust the lighting to reduce reflectivity and enhance contrast.
Oftentimes, it’s the substrate onto which the code is applied that most dramatically affects the contrast of barcode elements. To deal with uneven, noisy or highly reflective substrates, or poor distinction between the substrate and the mark due to shadows or mark depth, the critical component is lighting.
Lighting equipment can be tailored to the specific substrate to maximize contrast. While diffused lighting may help illuminate printed barcodes on glossy, flat surfaces, dark field lighting can apply low-angle beams of light to targeted regions of a substrate, enhancing the readability of embossed or engraved barcodes.
3. Consider using other types of barcodes and/or barcode readers.
Certain types of barcodes are more resistant to contrast problems than others. Linear (1D) barcodes such as UPC/EAN and stacked symbols such as PDF417 must be distinguishable across the entire length of the symbol to capture all critical elements. If any bars are obscured due to low contrast, the result can be a no-read for the entire code.
Since linear barcodes are typically longer, good contrast must be obtained for a large surface area, as opposed to 2D symbols such as Data Matrix and QR Code, which are typically more compact. Linear barcodes also require much higher contrast than 2D symbols – usually 80% or higher between light and dark elements – for the reader to acquire a uniform wave pattern.
In comparison, 2D imagers use cameras to capture images of 1D or 2D codes and require as little as 20% contrast between light and dark elements. For these reasons, using 2D symbols instead of 1D barcodes and, subsequently, 2D barcode imagers in barcode reading may decrease the possibility of unreadable codes due to low contrast.