Festo’s Solutions Prevent Contamination in EV Batteries
March 11, 2025
By Owen Hurst
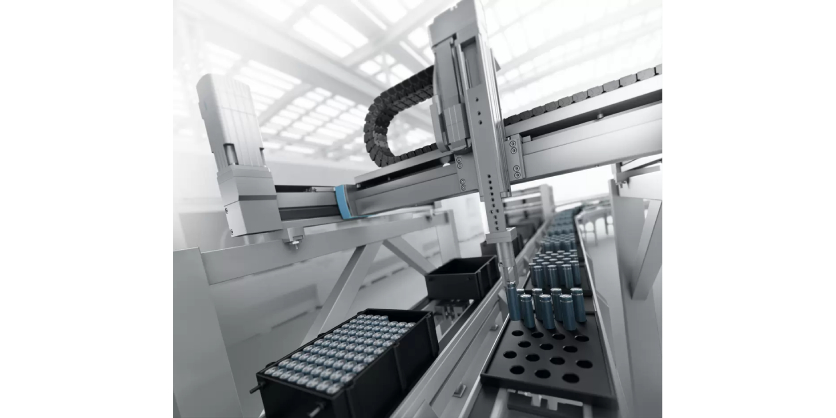
Festo’s Solutions Prevent Contamination in EV Batteries
Today, approximately 95% of electric vehicles (EVs) and energy storage systems use conventional lithium-ion batteries, which require liquid electrolyte filling. Lawrence Lin, Business Development Manager at Festo, specializes in automation advancements and technologies that drive improvements in productivity, quality, and safety through innovative designs. He says that safe and precise production is critical to ensuring the quality of a battery; any contamination can compromise its performance, lifespan, and safety.
“During the battery production’s formation stage, any contamination in the solid-electrolyte interphase (SEI) can lead to electrolyte breakdown during operation, potentially accelerating dendrite growth,” Lin says. “SEI is a thin protective layer that forms on the surface of the anode in lithium-ion batteries during the initial charging cycles, and it directly influences the battery performance, lifespan, and safety.”
“It is critical to prevent particle contamination because it can lead to electrical shorts and thermal runaway. Even the smallest metal particle contamination can create conductive pathways between the anode and cathode layers, causing internal short circuits. These shorts generate excessive heat, which can trigger thermal runaway. The most severe consequence occurs when dendrites reach the battery cell walls, potentially causing the cell to rupture, explode, and ignite a fire.”
Lin says that while there are currently no established industry standards for the manufacturing environment of battery cells, the general guideline is to maintain cleanliness equivalent to a Class 100 clean room (ISO 5). For reference, this environment permits a maximum of 100 particles smaller than 0.5 micrometers per cubic foot.
Moreover, Festo goes beyond the normal standard. They developed the Festo Guidelines, which provide a clear procedure for minimizing the risk of contamination by avoiding the use of non-ferrous metals. These guidelines have been established as a company-wide standard for all locations worldwide, ensuring the safe and reliable production of battery cells that ensures greater customer confidence in the product and lower reject rates for the manufacturer.
In fact, Festo’s F1A product portfolio was developed specifically for the requirements of battery production.
Lin says there is no single step in this process that is more (or less) susceptible to contamination. For instance, he says that metal shavings from manufacturing equipment are a common source of contamination – even within the cleanroom environment. “The overall cleanliness and use of non-ferrous metal-free components in the cleanroom manufacturing environment plays a critical role in preventing contamination before battery cells are sealed.”
The only way to detect if the battery cell has become contaminated is with ultrasonic testing. Lin says this process helps manufacturers identify problematic cells and sort them before they are assembled into modules for use. “Unfortunately, when contamination is detected inside the battery cells, they are not fixable and must be discarded, which can be costly. Therefore, the earlier the contamination is detected, the more cost effective it will be.”
The best practice is to avoid contamination altogether by using non-ferrous metal-free components to ensure clean production during the battery cell manufacturing process. Festo supports battery manufacturers by offering a wide range of products that are free of copper, nickel, and zinc, the metals that can contaminate the battery cell during manufacturing. These products ensure a clean production process and high-quality batteries that benefit both the manufacturer and the customer.
o know more visit Festo and if you enjoyed this article, you might also be interested in this free eBook.
Related Story
Battery Formation for EV Batteries: A Critical Step in Battery Production
Festo is a leading supplier of pneumatic and electrical automation technology, and they are supporting the Canadian automotive industry with innovative products, optimized motion control solutions, and unrivaled support. In this article, two subject matter experts from Festo, Jarod Garbe, Industry Segment Manager – Automotive, and Lawrence Lin, Emerging Technologies Business Development Manager -EV Batteries, shed more light on the subject. They discuss Festo’s products and solutions for EV battery production – with a particular focus on battery formation – arguably, the most critical part of the process.