Accelerating the Value of Data in Food and Beverage Processing
How to Navigate the Challenges and Opportunities of AI-Driven Advanced Process Control
March 5, 2025
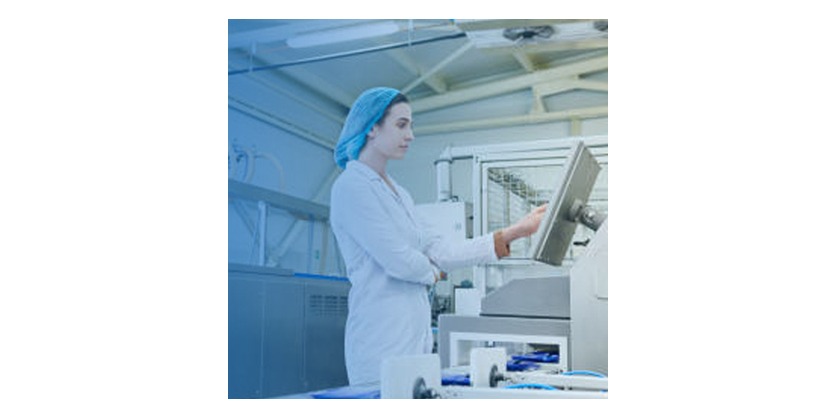
Accelerating the Value of Data in Food and Beverage Processing
The food and beverage industry is evolving faster than ever, and if you’re managing a production line, you’ve probably felt the pressure: more regulations, tighter margins, and shifting consumer demands. What if Artificial Intelligence (AI) could help your plant run smoother, faster, and more predictably with the value of data?
Implementing AI can feel like an uphill battle, from figuring out where to start, to justifying the investment. That’s exactly why Omron is here. This post breaks down the practical steps to plan, deploy, and manage AI solutions tailored to food and beverage operations.
The Current Gap Between Sensors and APCs in Food Processing
While many food and beverage processing plants have the necessary instrumentation to create process data, few are leveraging this data to its full potential. A recent McKinsey article states that while 75% of plants have instrumentation in place that controls critical process variables only 34% of plants have installed APC systems for crucial unit operations. These findings highlight the significant gap between potential and the reality of data within industry.
Planning for Intelligent Sensor Networks
To bridge this gap, food and beverage processors must plan for an intentional increase of sensor coverage. This involves establishing a clear scope by defining the specific processes that will benefit most from AI, ensuring that the pilot project is both stable and valuable. Empowering the production team by involving those closest to the production process in the planning and implementation stages ensures that the solutions meet the metrics that matter. Challenging the current architecture by avoiding the sunk cost fallacy and exploring new, more efficient technologies is crucial.
Choosing the Right APC Type
Currently we are seeing continued success with expert APCs. APCs focused on becoming an expert in a specific process rather than APCs that strive for general artificial intelligence. Within expert AI-based APCs, understanding the different types is important. Generative AI based advanced controls, trained with other algorithms or with synthetic data, may be best suited for producing unique process outputs. For instance, where a novel output is considered a feature and not a bug.
Building a Change Management Strategy
As we look forward to AI in advisory models, food manufacturers should define clear goals by understanding the unique value proposition and long-term objectives of the factory. Seeking advanced manufacturing partnerships with technology experts, like Omron, can complement in-house knowledge with technology expertise. Unifying the factory ecosystem by using globally open industrial protocols, such as IO Link, and controllers with built-in database connectivity. Food and beverage processors can ensure the creation and consumption of data is reliable, valuable, and deterministic.
Conclusion
The path to AI in advisory models is the result of a data first culture. Building a network of sensors that provides a perspective of key processes and unifying the factory floor is key. This positions food and beverage processors to pilot, then scale advanced process control that help teams run more efficiently.
More Information
Food, Beverage, and Commodities Automation
Related Story
Enhancing Food and Beverage Manufacturing with Motion Control
Key factors of motion control, such as servo position accuracy, trajectory repeatability, and system efficiency are essential for maintaining high performance and competitiveness. OEMs must balance the addition of advanced features with profitability, ensuring their equipment meets customer expectations and optimizes production processes.
This blog will explore the lifecycle of food and beverage manufacturing equipment—from design to production—highlighting best practices in motion control that enhance reliability and system performance, while keeping future technology integrations seamless and non-intrusive.