What is a Robotic Subsystem?
February 11, 2025
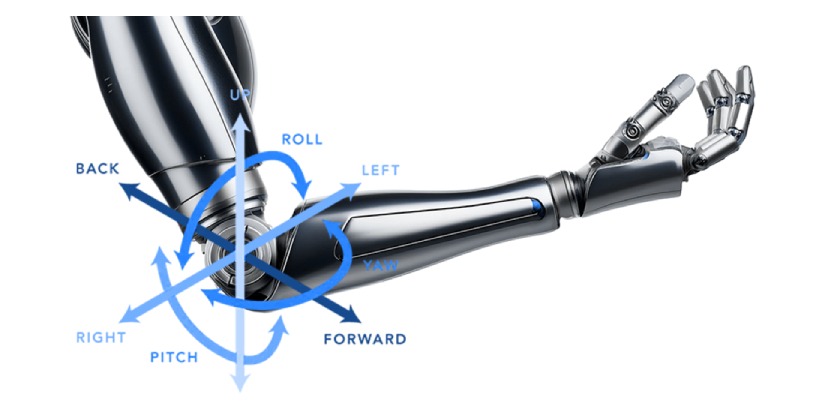
In robotics, a subsystem refers to a distinct functional unit within a robot, each responsible for specific tasks that contribute to the robot’s overall operation. Understanding these subsystems is crucial for designing, analyzing, and optimizing robotic systems.
This guide delves into the primary subsystems commonly found in robots, detailing their components and functions.
Mechanical Structure Subsystems
The mechanical structure subsystem forms the backbone of any robot. Rather than focusing on the entire structural system, the emphasis here is on the distinct subsystems that comprise it, such as joints, links, and end effectors.
These subsystems work together to define the robot’s physical capabilities, including range of motion, load capacity, and task-specific adaptability.
Key Mechanical Structure Subsystems
- Links: These rigid structures connect the joints and support the robot’s movement. Depending on the application, links can vary in material and design. For example, aluminum links offer lightweight precision for fast-moving arms, while steel links support heavy-duty industrial robots.
- Joints: These pivotal points enable movement between links, providing the robot with degrees of freedom (DOF). Key joint types include:
- Rotational Joints: Enable angular movement (e.g., in robotic arms).
- Prismatic Joints: Provide linear sliding motion (e.g., in Cartesian robots).
- Spherical Joints: Allow multi-directional rotation.
- End Effectors: The tools at the robot’s endpoint that perform specific tasks. Examples include grippers, welding heads, and suction cups. Robotiq’s ePick grippers, for instance, provide reliable handling for delicate materials in pick-and-place tasks.
Example Subsystems in Mechanical Structures
- Serial Joints: Found in robotic arms, each joint’s movement impacts the next, creating a chain-like kinematic effect. Universal Robots’ collaborative arms utilize such subsystems for flexible manipulation.
- Parallel Mechanisms: Delta robots employ multiple joints working together to deliver precision and speed in pick-and-place operations.
Drive Subsystems
Drive subsystems convert energy into mechanical motion, enabling specific robotic components to function efficiently. Rather than considering the drive system as a whole, this section focuses on motors, gearboxes, and actuators as modular subsystems.
Key Drive Subsystems
- Motors: Electric motors like Maxon’s EC frameless series integrate into joints, providing precision and compact design for robotic arms.
- Gearboxes: Essential for optimizing torque and speed. Harmonic Drive’s gear systems are well-suited for high-torque density applications in robotic joints.
- Actuators: These translate energy into physical movement. Maxon’s robotic actuators enhance servo performance for demanding tasks.
Example Subsystem Configurations
- Rotary Actuators: Used in articulated joints for precise angular motion.
- Linear Actuators: These are found in Cartesian robots or gripper mechanisms that require straight-line motion.
Focusing on these subsystems gives engineers the building blocks for optimizing robotics performance based on specific tasks.
Perception Subsystems
Perception subsystems allow robots to sense and respond to their environment and internal conditions. These subsystems include specific sensors integrated into joints, arms, and other components, rather than a generalized perception system.
Key Perception Subsystems
- Internal Sensors: Critical for monitoring a robot’s internal operations:
- Encoders: Embedded in joints to measure angles, speeds, and positions precisely.
- Current Sensors: Integrated into motors or actuators to track electrical performance and prevent overheating.
- External Sensors: Enable robots to perceive their surroundings:
- Vision Subsystems: Cameras and processors integrated into end effectors for object recognition and alignment.
- Force Subsystems: Load cells in grippers measure forces for delicate handling.
- Proximity Sensors: Often embedded into robotic arms for collision detection.
Subsystem Applications
- Joint Feedback: Encoders within rotary joints provide real-time positioning for precise motion.
- Object Recognition: Vision subsystems like Zivid’s 3D cameras enhance bin-picking operations.
- Force Control: Robotiq’s sensors ensure consistent pressure in material handling tasks.
Focusing on these perception subsystems highlights their role as integral components in larger robotic designs, allowing for tailored solutions across applications.
Control Subsystems
Control subsystems act as a robot’s brain, processing data from perception subsystems and sending precise commands to drive subsystems. These control units are critical for ensuring robots perform tasks accurately, safely, and efficiently.
Key Control Subsystems
- Motion Controllers: Manage the movement of individual joints or actuators. For example, Kollmorgen’s PCMM2G controllers provide high-performance motion control for complex robotic applications.
- Feedback Loops: Incorporate sensor data from encoders and current sensors to adjust movements in real time. Closed-loop systems ensure precise positioning and fault correction.
- Embedded Processors: Handle computational tasks such as signal processing, path planning, and decision-making. These processors are often integrated into servo drives or external control units.
Subsystem Applications
- Path Planning: Embedded processors compute optimal trajectories for robotic arms or mobile platforms, ensuring efficient movement.
- Collision Avoidance: Feedback loops enable real-time adjustments based on data from proximity sensors.
- Multi-Axis Coordination: Motion controllers synchronize movements across multiple joints or actuators to execute complex operations.
By focusing on individual control subsystems, engineers can tailor solutions to meet the requirements of specific robotic applications, enhancing precision, adaptability, and overall performance.
Human-Robot Interaction Subsystems
Human-robot interaction subsystems provide the interface through which humans can monitor, program, and control robots. These subsystems are critical for tasks like setup, debugging, and real-time control, ensuring effective communication between the user and the robot.
Key Interaction Subsystems
- Teach Pendants: Handheld devices that allow operators to program and guide robots manually. Universal Robots’ teach pendants are a prime example of intuitive design, enabling engineers to quickly adjust motion paths and test functionality.
- Control Panels: Stationary interfaces integrated into robotic workstations for continuous monitoring and adjustment. These panels often include emergency stop buttons, status displays, and manual override controls.
- Graphical User Interfaces (GUIs): Software-based interfaces accessible via tablets, computers, or mobile devices. They visually represent the robot’s operations, making it easier to configure and troubleshoot.
Subsystem Applications
- Programming: Teach pendants and GUIs simplify the creation of motion sequences and task-specific behaviors.
- Monitoring: Control panels provide real-time data on robot performance, enabling operators to identify and address issues immediately.
- Manual Control: Teach pendants allow operators to manually guide robots through complex tasks before automating them.
Human-robot interaction subsystems are essential for maximizing robot usability and adaptability, ensuring operators can efficiently program, monitor, and control robotic systems across diverse applications.
Power Supply Subsystems
Power supply subsystems provide the energy needed to operate all other robotic subsystems. These subsystems are designed to ensure reliable and efficient power delivery, tailored to the robot’s operational demands and environmental constraints.
Key Power Supply Subsystems
- Battery Modules: These are used in mobile robots and collaborative robots (cobots) where tethered power is impractical. They often include lithium-ion technology for high energy density and durability.
- Power Converters: Regulate voltage and current to ensure optimal performance for sensitive components like sensors and processors.
- Uninterruptible Power Supplies (UPS): Provide backup power to prevent operations disruptions, which is critical for industrial robots in automated production lines.
Subsystem Applications
- Mobile Robots: Battery modules power autonomous guided vehicles (AGVs) and drones, enabling extended operation without recharging.
- Industrial Robots: Power converters stabilize energy delivery for precision tasks requiring consistent performance.
- Critical Operations: UPS units safeguard against power outages, ensuring seamless operation in high-stakes environments like medical robotics.
The power supply subsystem is fundamental to a robot’s functionality. It ensures that all other subsystems receive the energy they need to perform effectively and efficiently.
Examples from Industry Partners
Our partners offer components that enhance various robotic subsystems, ensuring optimal performance and adaptability across applications:
- Maxon: Provides precision electric motors ideal for drive subsystems. For instance, the Maxon ECX SPEED 19 motor enhances high-speed robotic joints, offering superior reliability in assembly applications. Learn more here.
- Harmonic Drive: Specializes in gear systems that improve mechanical subsystems by delivering high torque and precision. The CSG Series Component Set is frequently integrated into articulated robotic arms to maximize torque density and minimize backlash. Discover more here.
- Kollmorgen: Offers advanced motion control solutions, including servo drives and controllers. The AKD2G Servo Drive simplifies integration while ensuring multi-axis coordination for robotic arms. Explore more here.
These examples demonstrate how industry-leading components empower robotic subsystems to achieve high performance and reliability in diverse applications.
Robotic subsystems form the foundation of every robotic application, with each component working harmoniously to deliver precision, efficiency, and adaptability. By understanding the role of mechanical structure, drive, perception, control, human-robot interaction, and power supply subsystems, engineers can optimize designs to meet specific operational needs. With industry-leading solutions from partners like Maxon, Harmonic Drive, and Kollmorgen, these subsystems empower advanced robotics across diverse industries, ensuring reliability and innovation in automation.