Everything You Need to Know About Grippers from Festo
December 13, 2024
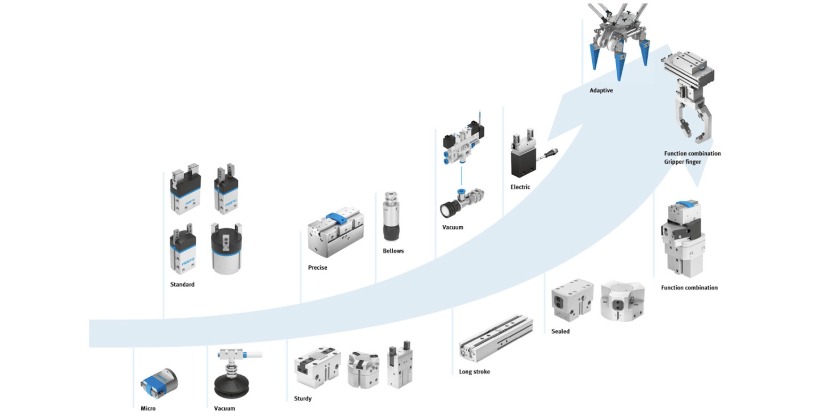
By Krystie Johnston, Cory Knight, and Ryan Kroger
Selecting the right gripper for an automated handling task can be challenging – but with Festo, it can be easier than ever to overcome these challenges.
Grippers are essential components of industrial robots and handling systems because they are the connection between the handling system and the workpiece. Grippers function using pneumatics, electrical power, vacuum, or a combination thereof to manipulate the workpiece or tool and achieve their desired task. Festo has a vast portfolio of grippers and accessories to support automated handling applications across a range of industries.
Cory Knight, Global Concept Engineer at Festo, and Ryan Kroger, Mechanical Design Engineering Manager at Festo combine their knowledge and experience with grippers to present everything you need to know about grippers: the different types, best practices for integrating them into automation systems, and tips for optimizing their performance. They also discuss support from Festo that makes selecting the best gripper as easy as possible.
Types of Robotic Grippers
Festo’s grippers can be grouped into three categories: mechanical, vacuum, and universal (also known as soft or adaptive grippers). Knight and Kroger say that each type of gripper has its unique features and benefits. Looking at each type in turn, they highlight their attributes and point out some of the typical automated handling applications they are best suited for.
Mechanical Grippers
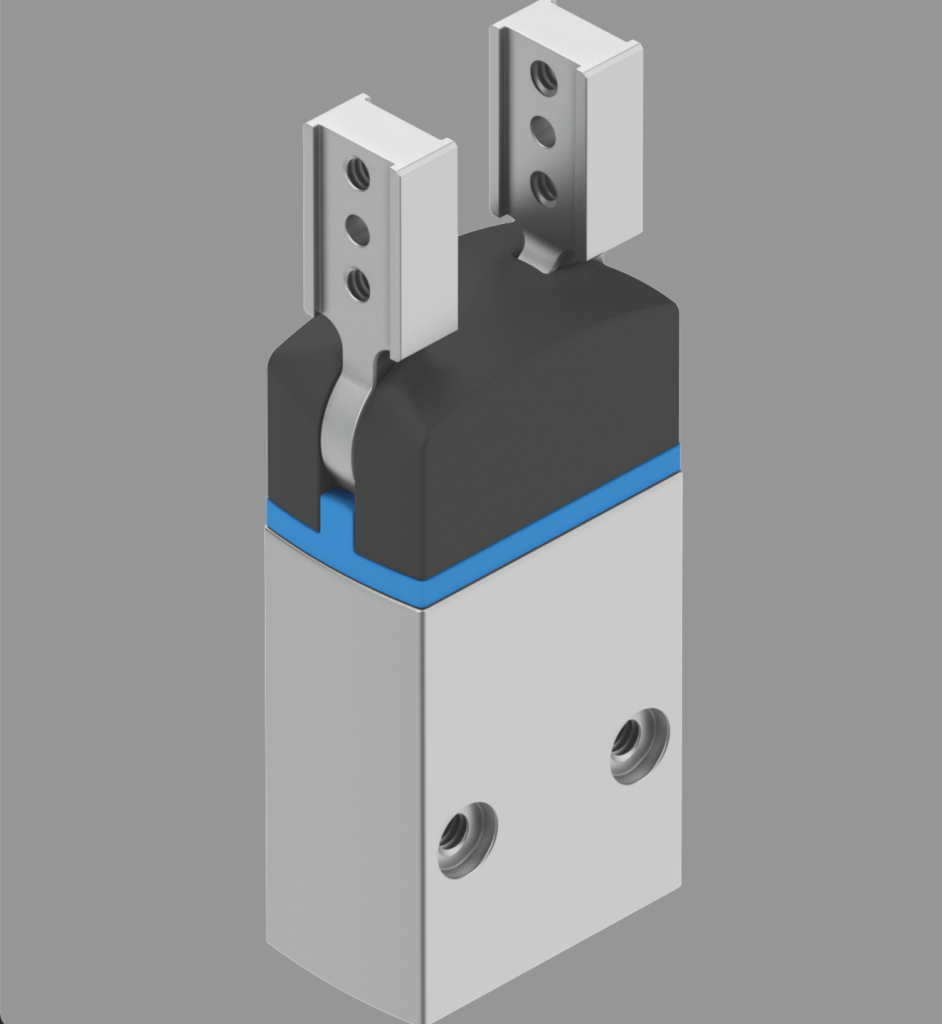
Mechanical grippers are commonly used in industrial automation and manufacturing processes. They are suitable for handling objects with defined shapes and sizes. Applications include pick-and-place operations, assembly lines, packaging, and material handling in industries such as automotive, electronics, end of line packaging and intralogistics.
Mechanical Gripper Features:
- Mechanical Actuation: Operated through mechanical means, such as gears, levers, compressed air, or springs, without the need for external electrical power sources.
- Variety of Designs: Available in various configurations, including parallel, angular, radial, concentric and multi-finger grippers, to accommodate different shapes and sizes of objects.
- Robustness: Designed to withstand harsh environments and heavy loads, making them suitable for industrial applications which require millions of cycles.
- Customizable Jaws: Jaws can often be customized or replaced to suit specific gripping needs.
Mechanical Gripper Benefits:
- High Speed: Quick actuation increases productivity by reducing cycle times in manufacturing processes.
- Strong Grip: Capable of handling heavy loads due to the powerful force generated by pneumatic systems.
- Versatility: Suitable for a wide range of applications, from assembly and packaging to material handling.
- Reduced Risk of Damage: Adjustable gripping force allows for careful handling of fragile items, minimizing the risk of damage.
- Energy Efficiency: When designed properly, mechanical gripping systems can be energy-efficient, especially in high-speed applications.
Vacuum Grippers
Vacuum grippers utilize suction to hold and manipulate objects. Traditional vacuum cups are ideal for handling objects with smooth, flat surfaces, such as glass, metal sheets, and corrugated cases. Festo also offers specialty vacuum cups (Foam and Bernoulli grippers) for rougher surfaces, delicate, and porous workpieces. Vacuum grippers find applications in industries like logistics, warehousing, food processing, and packaging. They are often used in automated systems during primary, secondary, and tertiary packaging.
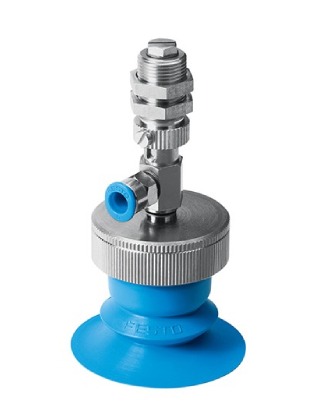
Vacuum Gripper Features:
- Vacuum Generation: Utilize vacuum suction to grip objects, typically created by a vacuum pump or venturi system.
- Flexible Suction Cups: Equipped with various types and sizes of suction cups that can conform to different shapes and surfaces.
- Lightweight Design: Often designed to be lightweight, which can enhance the efficiency of robotic arms and reduce energy consumption.
- Quick Release: Allow for rapid release of objects, facilitating fast-paced operations.
- Sensor Integration: Can be fitted with sensors to monitor grip status and detect the presence of objects.
- Multiple Configurations: Available in different configurations, including single and multi-suction cup designs, to accommodate various applications.
Vacuum Gripper Benefits:
- Versatility: Effective for handling a wide range of materials, including flat, smooth, and porous surfaces.
- Gentle Handling: Ideal for delicate items, as vacuum grippers can provide a soft touch without damaging the surface.
- Increased Efficiency: Fast and reliable gripping and releasing capabilities enhance productivity in automated processes.
- Adaptability: Can easily adapt to different shapes and sizes of objects, making them suitable for diverse applications.
- Reduced Need for Mechanical Parts: Fewer mechanical components can lead to lower maintenance requirements and increased reliability.
- Cost-Effective: Often more economical than other gripping technologies, especially for high-volume applications.
Adaptive Grippers
Adaptive grippers can adjust their shape or grip according to the object being handled. They are versatile and suitable for handling objects of various shapes, sizes, and materials. Adaptive grippers find applications in industries such as robotics, food & packaging, Industrial Automation and Logistics. They are used in tasks like grasping irregular objects, delicate handling, and collaborative robot applications.
These gripper systems are currently being used in a wide range of industries, including automotive, electronics, logistics, Life Science, Food Processing and Packaging, Injection Molding and many more. The specific applications vary depending on the industry and requirements of the task. It is important to note that the use of gripper systems is not limited to these industries, and their applications continue to expand as automation technology advances.
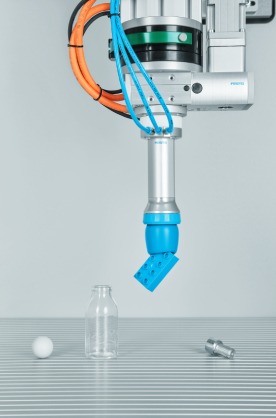
Adaptive Gripper Features:
- Versatility: Capable of handling a wide range of objects, making them suitable for diverse applications in various industries.
- Reduced Risk of Damage: The soft, adaptive nature allows for gentle handling of delicate items, minimizing the risk of damage.
- Increased Efficiency: Quick adaptability to different objects can streamline operations and reduce cycle times.
- Improved Grip Reliability: Enhanced feedback mechanisms ensure a secure grip, even on challenging surfaces or shapes.
- Cost-Effective: Can reduce the need for multiple specialized grippers, saving costs in equipment and maintenance.
- Enhanced Automation: Their ability to adapt to varying tasks makes them ideal for automated processes, improving overall productivity.
- Part Positioning Compliance: The soft fingers provide compliance when parts are being picked or placed, e.g. picking a polymer part from the IMM during ejection
Adaptive Gripper Benefits:
- Flexible Jaws: Equipped with soft, flexible jaws that can conform to the shape of the object being gripped.
- Sensor Integration: Often include sensors (like force, pressure, or vision systems) to provide feedback on grip status and object characteristics.
- Multi-Finger Design: Typically features multiple fingers or gripping points that can adjust independently to grasp irregularly shaped items.
- Advanced Control Systems: Utilize sophisticated control algorithms to adapt grip strength and position in real-time.
- Lightweight Materials: Made from lightweight materials to enhance efficiency and reduce the load on robotic arms.
- Modular Components: Many adaptive grippers are designed to be modular, allowing for easy customization and replacement of parts.
Integrating Robotic Grippers into Automation Systems
Kroger says the connection of gripper systems to the end-user’s process or application depends on the specific requirements and setup of the system. Grippers can have a variety of different control interfaces that include digital inputs/outputs (I/O), analog inputs/outputs, or serial communication ports. Multiple communication protocols are offered for customers. For example, HEPP can be controlled via PROFINET®, EtherNet/IP®, and EtherCat®.
He says the integration of gripper systems into the end-user’s process or applications is typically performed by system integrators or automation engineers. Festo supports them by providing a range of accessories and tools to enhance the performance and functionality of their grippers and gripper systems. These accessories may include jaw blanks, adapter mounting plates, sensor integration kits, connection cables, and additional pneumatic or electrical components, which enables users to customize and optimize their gripper systems for specific applications.
Kroger says that Festo also offers comprehensive support for integrating their grippers and gripper systems into larger automation systems. This includes technical documentation, programming assistance, native CAD files with constraints, and training resources to ensure smooth integration and operation of the gripper systems within the overall automation setup.
Festo’s Universal Robot Kits
To get a collaborative handling system up and running as easy as possible, Kroger says Festo’s Universal Robot (UR) kits offer a convenient plug-and-work solution for integrating Festo grippers with Universal Robots. These kits come complete with all the essential mechanical and electrical interfaces required for seamless integration with a Universal Robot. Additionally, the kits include a corresponding software plug-in and sensors, enabling quick and hassle-free commissioning.
By providing these comprehensive kits, Kroger says Festo significantly reduces startup efforts and streamlines the integration process. The UR kits are available in different variants, including mechanical, vacuum, and adaptive kits, catering to a wide range of applications and handling requirements.
Optimizing Gripper Performance
Optimizing gripper performance makes the automated handling system as efficient and productive as possible. To help with this, Festo offers a variety of different sizing tools that are available for free on their website. Kroger says these sizing tools include Vacuum Design, Gripper Sizing, Three-point gripper, Angle Gripper, and Radial Gripper selections. These sizing tools guide users through a series of questions and options to narrow down the available gripper options. He says users can input parameters such as load capacity, gripping force, stroke length, and other relevant factors to find the best gripper for their application.
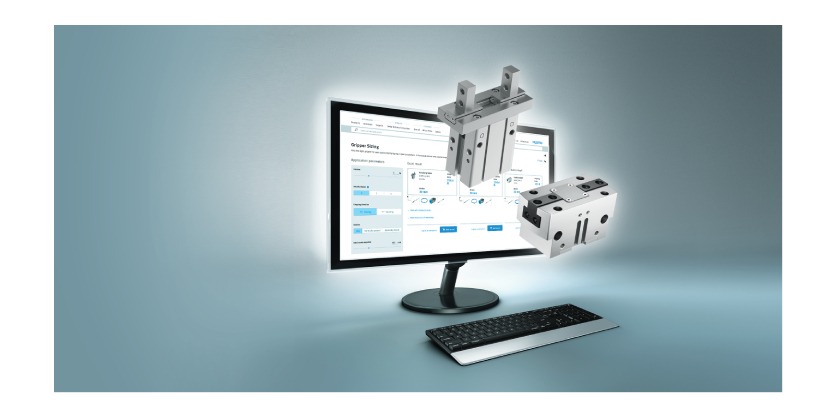
To effectively use these tools, Kroger says users need to provide relevant information such as the type of objects to be handled, weight and dimensions of the objects, required gripping force, environmental conditions, and any specific application constraints. The more detailed and accurate the information provided, the better the tool can recommend suitable gripper options.
Kroger adds that Festo continually refines these tools to enhance their accuracy, user-friendliness, and compatibility with the latest gripper offerings to provide users with the most up-to-date and reliable information for selecting the best gripper for their application.
And he adds that Festo also has a global network of gripping experts; if additional assistance is needed, they are always ready to offer that support.
Misconceptions (and Realities) About Selecting Grippers
As the lead of the Mechanical Engineering team at Festo’s Technical Engineering Centre in Mason, Ohio, Kroger and his team focus on new product development and customization of existing product catalogues to meet specific customer applications. As a Mechanical Engineer, one of his specialties focuses on product design and gripping or end of arm tooling applications.
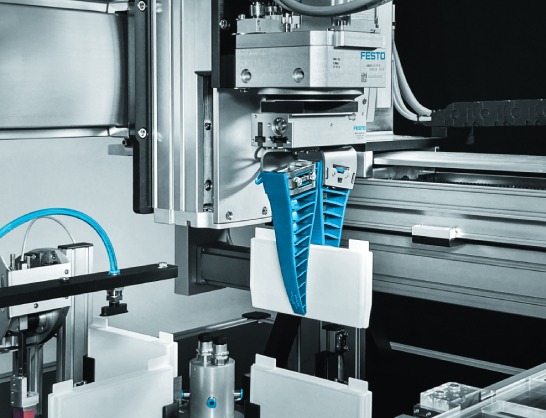
Kroger says one misconception he sees customers make when selecting a gripper is assuming that a single gripper can handle all types of objects and applications. Different grippers are designed for different purposes. For example, mechanical grippers are best suited for rigid objects, vacuum grippers are ideal for flat and smooth surfaces, and adaptive grippers are good for handling objects of varying shapes. Understanding the specific handling requirements when selecting the appropriate gripper type is crucial.
As a Concept Engineer on Festo’s Global Engineering team, Knight and his team focus on the food and beverage and end of line packaging industry segments. He has worked extensively with food manufacturers and original equipment manufacturers, providing engineering support related to the development of new systems and new technologies.
Knight lays out some of the most common misconceptions he sees when people begin the process of selecting a gripper and provides insights to improve the selection process.
Underestimating Grip Force:
- Misconception: Some people assume that any gripper will provide sufficient grip force for their application.
- Reality: It is crucial to calculate the required grip force based on the weight and friction of the object to avoid slippage. The required grip force is also dependent on the type of gripper finger used in the application, for example, encapsulated grip or friction grip.
Overlooking Environmental Factors:
- Misconception: Customers might not consider environmental conditions, such as temperature, humidity, or exposure to dust and debris.
- Reality: Gripper materials and designs must be compatible with the operating environment to ensure reliability and longevity.
Neglecting Integration Requirements:
- Misconception: Some believe that any gripper will seamlessly integrate with their existing systems.
- Reality: Compatibility with robotic arms, control systems, and other equipment should be considered during selection.
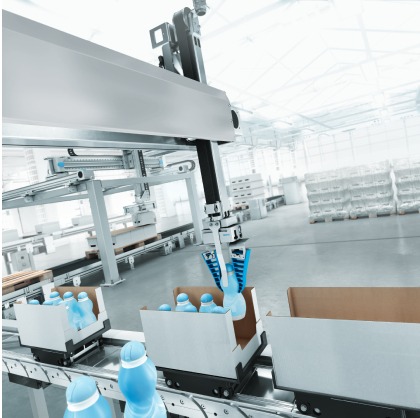
Assuming Higher Cost Equals Better Performance:
- Misconception: There’s a belief that more expensive grippers are inherently better.
- Reality: The best choice depends on specific application needs rather than price; a less expensive option may be more suitable.
Not Considering Future Needs:
- Misconception: Customers often focus solely on current requirements without considering future applications or changes.
- Reality: Selecting a versatile or adaptable gripper can save time and costs in the long run. Also, carefully considering the ability to sense multiple grip positions and the technology used to control the gripper can help in future proofing the gripper selection.
Overlooking Maintenance Needs:
- Misconception: Some assume all grippers require the same level of maintenance.
- Reality: Different gripper types have varying maintenance requirements, which should be factored into the decision.
Expert Advice for Selecting the Best Gripper for Your Application
Selecting or sizing grippers requires an understanding of force and torque. If not considered properly, the result could be an automated handling system that does not work properly.
Kroger says gripping force refers to the amount of force exerted by the gripper to securely hold an object and that it should be appropriate for the weight and characteristics of the objects being handled. He warns that insufficient gripping force may result in objects slipping or dropping, while excessive gripping force can damage or deform the objects. He emphasizes that it is important to select a gripper with the appropriate gripping force to ensure reliable and secure handling.
He explains that the payload capacity of a gripper is closely related to its gripping force. He says that it represents the maximum weight that the gripper can effectively handle without compromising performance or safety. It is essential to consider the weight of the objects being handled and choose a gripper with a suitable payload capacity to avoid overloading the gripper or causing instability during operation.
And Kroger adds that torque comes into play when the gripper needs to rotate or twist objects during handling. He says grippers equipped with rotational capabilities, such as Festo’s EHMD rotary gripper module, require sufficient torque to manipulate objects effectively. Therefore, the torque capacity of the gripper should be considered when selecting a gripper for applications that involve rotation or twisting actions. Additionally, torque is applied to grippers when the tool is accelerated in the horizontal direction. High acceleration loads and long gripper fingers can result in high torque values which must be considered in the selection process.
Festo’s Online Shop – Another Tool to Help You Succeed
Knight and Kroger unanimously agree that Festo’s online shop is a great resource to help people select the best products to achieve their automation requirements. Festo’s online shop allows customers to conveniently browse and purchase their products and components online. The online shop offers 24/7 accessibility, allowing customers to browse and purchase Festo products at their own convenience. It also simplifies the ordering process, provides detailed product information, and offers access to technical documentation and support, enhancing the overall customer experience.
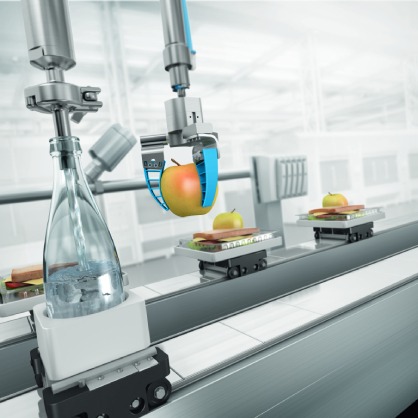
Features of Festo’s Online Shop
- User-Friendly Interface: An intuitive design that makes it easy to navigate and find products.
- Comprehensive Product Catalog: A wide range of products, including automation technology, pneumatic components, and more.
- Search and Filter Options: Advanced search functionalities to quickly locate specific items based on various criteria.
- Detailed Product Information: Access to specifications, technical data (such as CAD models), and application examples for informed purchasing decisions.
- Online Ordering: The ability to place orders directly through the platform, often with options for bulk purchasing.
- Account Management: Features that allow users to manage their accounts, track orders, and view purchase history.
- Support Resources: Access to manuals, catalogs, and technical support to assist customers in their purchasing process
Benefits of Festo’s Online Shop:
- Convenience: 24/7 access to the shop allows customers to place orders at their convenience without time restrictions.
- Time Savings: Streamlined ordering processes help reduce the time spent on procurement.
- Cost Efficiency: Online promotions and bulk purchasing options can lead to cost savings for businesses.
- Quick Access to Information: Immediate access to product details and specifications helps customers make informed decisions.
- Enhanced Customer Support: Online resources and support can assist customers in troubleshooting and product selection.
- Order Tracking: Ability to track orders in real-time, providing transparency and peace of mind.
Conclusion
With all the choices available when it comes to selecting a gripper for your automated handling application, it can be challenging to figure out which one is best for your application. Festo makes it easier than ever to help you overcome these challenges with their vast portfolio of grippers, accessories, online tools, and support.
More Information
Interested in Learning More? Visit Festo or download their latest Gripper eBook that explores the current and future trends of gripper technologies in automated handling applications.