Proax Technologies’ Commitment to Combatting Forced and Child Labour
June 5, 2024
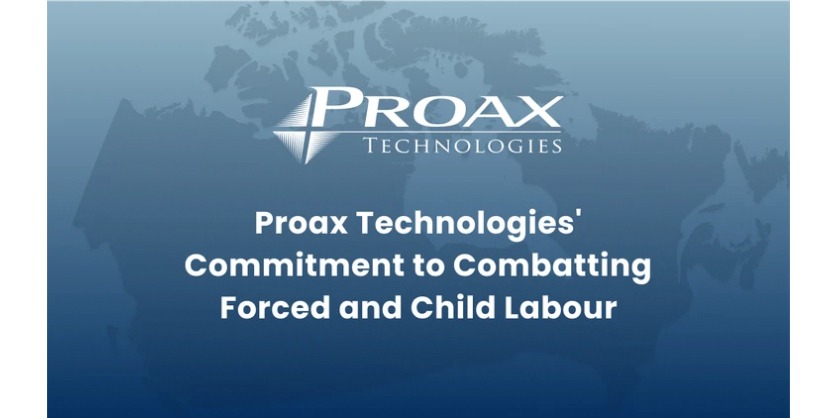
Statement on Forced Labour and Child Labour in Supply Chains for the Financial Year ended June 30th 2023
This statement is made pursuant to Bill S-211, An Act to enact the Fighting Against Forced Labour and Child Labour in Supply Chains Act and to amend the Customs Tariff. This statement outlines the approach and initiatives by Proax Technologies Ltd to identify and address the risks forced labour and child labour in its business operations and supply chains during the financial year commencing July 1st, 2022, and ending June 30th 2023.
Proax Technologies has been guided by certain basic principles about the people to whom we are responsible and whose trust we want to earn. Chief among these are integrity, responsibility, and respect. We have a zero-tolerance policy for human trafficking or slavery, and we unequivocally support the human rights of our workforce and the workforce of our global suppliers.
Proax Technologies is firmly committed to protecting individuals from the exploitations of illegal labour practices such as child labour, forced labour, slavery, and human trafficking; such practices will not be tolerated. Proax Technologies will hold itself accountable to the highest ethical standards and will comply with and exceed all relevant and applicable local and international laws pertaining to illegal labour practices. In doing so, Proax will not knowingly contract with, or carry on a business relationship with any organization or employer that does not adhere to the same standards or is in violation of any relevant or applicable labour laws.
In keeping with this commitment, we support the United Nations Declaration of Human Rights, the CGF Social Resolution on Forced Labour, its priority principles, and the International Labour Organization core standards on forced labor, child labor, freedom of association and discrimination. We also support all laws that seek to prevent and eliminate slavery and human trafficking from global supply chains by increasing transparency, including Canada’s Fighting Against Forced Labour and Child Labour in Supply Chains Act.
Group Structure
Proax Technologies Ltd (a family-owned Corporation) is a leading Canadian Technical Automation Distributor that offers innovative product solutions in the areas of Automation and Robotics, Motion Control and Machine Safety, creating close relationships with our valued customers, vendors, and employees. We’ve been in the marketplace for over 60 years, and we continue to grow and expand our product line and services to meet our customers’ needs. Our website can be found at www.proax.ca.
Currently Proax has over 200 employees with 13 branch locations in Canada coast to coast. Our key point of difference is our in-house technical solution team that enables us to provide solutions dedicated to customer specific product or solution needs. We have a team in all regions to assist with technical support across our entire range of products.
Proax Technologies is proud to represent world-class manufacturers in the industrial automation field, allowing us to offer customers the best possible products and solutions. With our highly trained staff, Proax offers top customer service and technical support. We are proud to be a preferred technical automation distributor!
Proax was established in 1962, and trades under the business name of Proax Technologies Ltd. Our head office is located at 6700 Millcreek Dr, Unit 3, Mississauga, Ontario L5N 8B3 and have the following branch locations:
- 10230, Grace Road, Surrey BC V3V 3V6
- 858 Century St., Winnipeg MB R3H 0M5
- 440 Advance Boulevard, Tecumseh ON N8N 5G8
- 555 Consortium Court, London ON N6E 2S8
- 405 Maple Grove Road, Unit #13, Cambridge ON N3E 1B6
- 21 Hooper Rd, Barrie ON L4N 9S3
- 1925 R. John-Molson, Laval QC H7T 0R3
- 834 Industriel Boulevard, Granby QC J2J 1A4
- 240, rue de Sydney, Suite 110 St Augustin de, Desmaures QC G3A 0P2
- 1 Austin Street, St. John’s NL A1B 4C1
- 109 Ilsley Avenue, Unit 17, Dartmouth NS B3B 1S8
- 2880 45 Ave SE Unit #156, Calgary Alberta T2B 3M1
Proax has adopted a matrix organizational structure which has encouraged open communication between departments, locations, and creates better sharing of skilled resources. It has also placed management team members in different branch locations creating better leadership throughout the company.
Our Company culture is an integral part of our business, and we are very proud of our unified corporate culture “OneProax”. Having several locations across Canada, we work hard to maintain a respectful workplace in which we share common values and encourage input from employees. The company mission and values are clear, communicated often, and embraced. Our employees are important to the overall growth of the company, and we appreciate everyone’s dedication and hard work.
Supply Chain
Given the highly specialized products Proax distributes, there are a limited number of global suppliers available with the expertise needed to manufacture to the specifications demanded by Proax and its customers. Thus, Proax’s supply chain is limited to a very small number of highly sophisticated and mature top-tier global manufacturers.
These global manufacturers primarily operate in developed countries with robust and stable government and regulatory bodies with strict business and social governance and compliance structures. These countries include: the United States, Canada, Japan and EU Member Countries.
Although Proax offers many technical, design, assembly and engineering services, its supply chain process is generally limited to the purchase of finished goods directly from the suppliers previously noted.
Risks in Supply Chain
Given the nature and limited number of Supplier’s, there are no material risks regarding forced labour and child labour in first tier of Proax’s supply chain.
Again, given the nature and limited number of Suppliers, there is also low risk regarding forced labour and child labour in the lower tiers of Proax’s supply chain.
Actions Taken
Proax has taken the following actions:
- Conducted a strict assessment and acceptance threshold of all material suppliers. As previously discussed, very exclusive and selective partnering is key to Proax’s efforts to ensure its supply chain is free of and resistant to forced labour and child labour.
An extensive review of all material suppliers has been conducted and it was found that all material suppliers have regulations, policies, and procedures in place to address forced labour and child labour within their organizations. These regulations, policies and procedures include compliance with related legislative frameworks including:
- UK Modern Slavery Act 2015
- the Australian Modern Slavery Act 2018 o the German Supply Chain Act (GSCA)
- the United Nations Universal Declaration of Human Rights
- the United States Fair Labor Standards Act
- the OECD Guidelines for Multinational Enterprises
- the core labour standards of the International Labour Organization (ILO)
- the United Nations Guiding Principles on Business and Human Rights
To further mitigate risks lower in Proax’s supply chain, Proax has ensured that the regulations, policies and procedures used by suppliers are applied to lower levels of the supply chain through mechanisms such as Supplier Codes of Conduct and whistleblower mechanisms.
In the event a supplier, vendor or contractor was found to be in violation of this policy, Proax would take prompt remedial action in order to address the violation, remedial measures may include termination of the business contract with the organization.
Proax Technologies shall continually monitor its own employment practices as well as those of its partners, vendors, suppliers, and all others conducting business on behalf of the organization in order to ensure compliance to ethical employment standards and protocols. In order to ensure compliance to the standards of this policy,
- Proax has audited and will continue to audit its own employment practices as well as those companies the organization contracts with or maintains a business relationship with.
- Continue to fostered our company culture which supports human rights and non-discrimination.
- Conducted age verification in pre-hire interviews, training, and onboarding of new employees.
Remediation
Protecting victims of slavery is the most fundamental principle of any remediation. Proax acknowledges that, once an allegation of modern slavery is made, victims should be:
- Taken to a place of safety with appropriate security.
- Consideration for any vulnerabilities such as gender, disability, age.
- Provide reassurance and welfare (food, drink, medical assistance).
- Informed of what third parties are involved (if any).
- Proax will help to provide access to relevant government or third-party remediation services such as the police (if it is safe to do so) or other recognized remediation authority.
- Ensure that all personal data is kept confidential including evidence, records, and interviews.
- Monitor the victim’s progress.
- Once an incident has been reported, the company will investigate to determine whether the incident constitutes an act of modern slavery.
- Maintain incident reports, investigation findings.
Training
Our staff receives the following training:
- Onboarding training includes:
- Diversity, Equity & Inclusion
- Workplace Anti-Violence, Harassment & Sexual Harassment
- Proax Code of Conduct
- Learning Management System
- Annual training – Modern Slavery interactive course includes:
- What is modern slavery and who does it affect?
- Warning signs
- Business responsibilities
- Reporting methods
- Annual training – refresher courses:
- Diversity, Equity & Inclusion
- Workplace Anti-Violence, Harassment & Sexual Harassment
- Proax Code of Conduct
- Annual training – Modern Slavery interactive course includes:
Effectiveness Assessment
Given the strict assessment and acceptance threshold for suppliers has been completed for all material suppliers, Proax has obtained assurance that the vast majority of its supply chain is free of forced labour and child labour. This assessment process is highly effective.
Sign off
Human rights have always been a central component of our corporate culture and principles. As an independent family corporation, we focus on our Employees, our Vendors and Customers. This statement is made pursuant to Bill S-211, An Act to enact the Fighting Against Forced Labour and Child Labour in Supply Chains Act for the financial year ending June/30/2023. It has been issued on behalf of Proax Technologies Ltd and approved by the directors. Our small but important effort will help to make the world a better place.
Signed and Dated: May 27, 2024
Stephen Daub, President
Theresa Daub, Corporate Secretary
Related Story
Proax Earns Great Place to Work® Certification
Proax Technologies, a leading Technical Automation Distributor, is excited to announce it has once again received Great Place to Work® certification. This is the 6th year in a row they have received this certification. This announcement follows an extensive and independent analysis conducted by Great Place to Work Institute® Canada, based on valuable feedback provided by employees through an anonymous survey about their workplace experience.