Comau’s MATE-XT Wearable Exoskeleton Supports Ergonomic Well-Being At John Deere’s Parts Distribution Center In Brazil
April 28, 2023
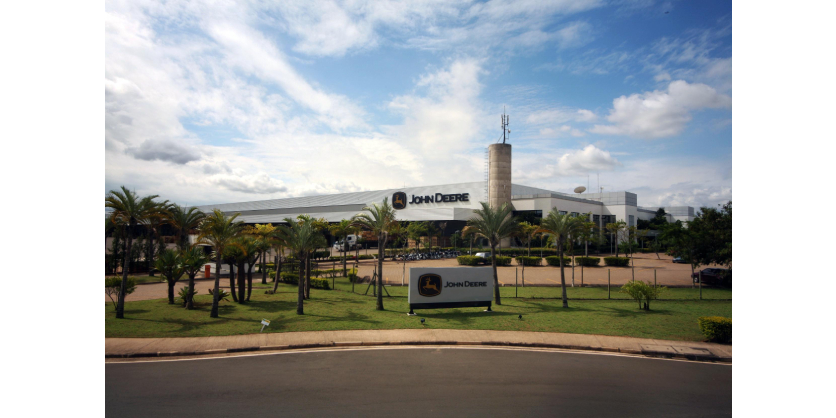
- John Deere has deployed multiple MATE-XT exoskeletons to further facilitate better ergonomic sustainability for its employees
- The wearable robotic device effectively reduces biomechanical risk by 50% based on electromyographic analysis while keeping muscle effort during manual activities at a rest state 98.5% of the time
- The slim, highly breathable exoskeleton provides comfortable, all-day ergonomically-assisted support aimed at increasing the quality and precision of repetitive tasks
- MATE-XT is water, dust, UV-light and temperature resistant, making it ideal for difficult applications and environments
Comau has equipped John Deere with multiple MATE-XT wearable exoskeletons to help sustain worker well-being, alleviate physical stress and reduce the ergonomic risk within its parts logistics operations. MATE-XT accurately replicates all movements of the shoulder, helping employees perform their jobs comfortably by reducing muscle fatigue without limiting mobility or adding bulk. Its ergonomic design can be easily adjusted to fit different people with different body types – changing the length of the shoulder straps and the required level of assistance based on the worker or the job at hand is quickly achieved in a few simple steps. Working closely with John Deere to implement the exoskeleton within its daily operations, Comau provided a hands-on training course held at John Deere’s 75,000m2 parts distribution center in Campinas, in the state of São Paulo.
As parts are often required for next-day delivery, John Deere’s employees must select, sort and package hundreds of parts per day, a task that involves repetitive movement of the arms, shoulders and back.
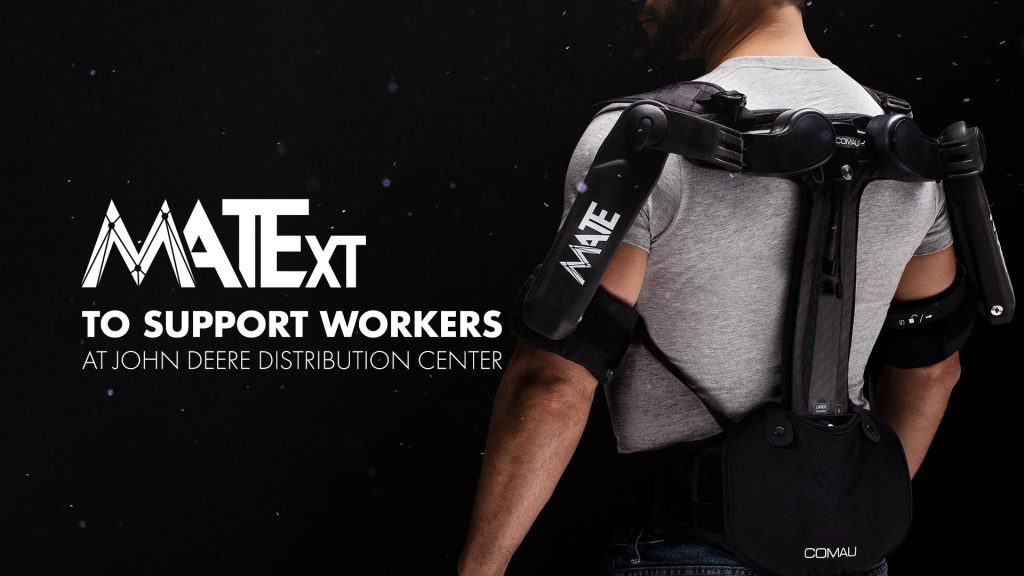
MATE-XT’s highly breathable design is worn like a backpack, providing comfortable, all-day ergonomically-assisted support aimed at increasing the quality and precision of manual tasks. In addition to offering highly effective postural support, MATE-XT is EAWS-certified (Ergonomic Assessment Work-Sheet), which enables John Deere to acquire an objective measurement of ergonomic improvement and projected benefits in terms of reduced muscle fatigue and execution speeds.
Even when working with small and lightweight objects, the apparently minimal effort of repeated manual movements can take a toll on the body. To help John Deere quantify the benefits of using MATE-XT, Comau performed an electromyographic analysis of the ergonomic risk factor. MATE-XT kept the muscle at a rest stage for 98.5% of the activity time (compared to only 2.4% of the time without MATE-XT).
Furthermore, Comau’s MATE-XT ensures proper muscular balance while optimizing the energy expenditure needed to stabilize and sustain the weight of the arm. Wearing the exoskeleton, arm stability can be maintained using only 10% of the operator’s maximum force capacity. This translates to an improved feeling of well-being in addition to tangible performance-based results such as process optimization and productivity gains. All said, MATE-XT is helping John Deere to mitigate ergonomic risks and achieve a 68% reduction in muscle overload.
“Our efforts to provide customers with innovative automation technologies extends to finding new ways to ensure their workers stay safe during their day-to-day activities, in different applications and markets,” said Laerte Scarpitta, Comau Leader for the Americas. “MATE-XT is an easy-to-use wearable exoskeleton that allows John Deere to provide greater added value and measurable benefits in terms of reducing perceived muscle fatigue and as a consequence, the mechanical stress on a worker’s back, lumbar region, arms and shoulders. It is yet another example of the value that robotics can bring.”
Laerte Scarpitta, Comau Leader for the Americas
More Information
Related Story
Comau Is Developing A New Mobile Robotics Solution Featuring Collaborative Robots In The Context Of 3 EU Projects
Comau is designing a powerful mobile robotics platform as part of an open, highly collaborative production environment, in the context of 3 different European Projects.
The integrated solution, which leverages Comau’s proven expertise in IoT-enabled technologies and collaborative robotics, is a natural evolution of the company’s automated workflow optimization systems. Modular, scalable and completely re-configurable, the platform can be easily adapted to different applications without changing the system’s underlying software or hardware architecture. Furthermore, because the robotic arm is mounted on an autonomous mobile platform it is not tied to a single operation but can address a large number of applications in different areas of the plant as needed.