Nidec Machine Tool to Unveil a New Nozzle with the Largest Gas Shielding Region in the World at formnext2022 in Frankfurt, Germany from November 15th to 18th
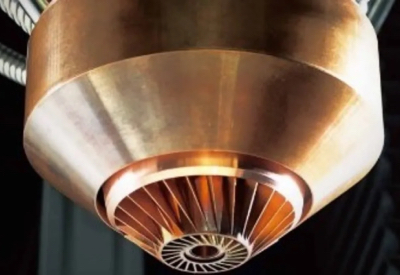
November 7, 2022
Nidec Machine Tool Corporation recently announced that it will exhibit its “LAMDA series” deposition-type (DED-type) metal 3D printers at Formnext2022, a metal 3D printer exhibition to be held in Frankfurt, Germany from November 15 – 18.
The new local shield nozzle improved a shielding region up to 45x larger
At this event, the Company will exhibit its own technologies, the local shield nozzle and the monitoring feedback system, both of which continue to evolve since their 2019 debut. Applying both technologies enables Nidec Machine Tool’s 3D printers to create large objects, stabilize their quality, and improve the accuracy of their shapes, all without installing a chamber. Furthermore, the technologies are highly practical in laminating dissimilar metals and making prototypes by using functional gradient materials. At Formnext2022, the Company will display samples that demonstrate the LAMDA series printers’ capabilities, and appeal them to aerospace, energy, and auto industries.
The samples (to be exhibited for the first time ever)
A high-precision additive fabrication sample modelled after a rocket engine is 500mm in diameter and has a wall thickness of 1mm
- 1. A design sample of a complex-shaped rocket engine nozzle (1/2 in size)
- 2. An aluminum alloy-based fabrication sample – one of the largest of its kind in the world
- 3. A cutting-edge local shield nozzle with improved shielding performance
Utilizing the 5-axis additive fabrication technology and the monitoring feedback function to create large, complex-shaped components with high accuracy
Using LAMDA2000, a larger 3D metal printer, to fabricate a 1,160mm tall shape of aluminum alloy The optimized shield gas spraying function expands the shield region area by a factor of 45 compared with those of conventional products.The LAMDA series’ features
- 1. The powder DED method is a technology to consecutively spray powder from a nozzle, and irradiate the powder with a laser to melt/coagulate it. This technology can create a shape more than 10 times faster than the powder bed method, which creates a shape by filling a tank (bed) with metal powder. With no need to use a metal powder tank, the powder DED method can create large shapes that the powder bed method cannot. Equipped with the local shield function and the monitoring feedback function that were exclusively developed for them, the LAMDA series printers can create large components – one of the DED’s features – with high quality.
- 2. The local shield function, which eliminates oxygen in an ambient environment during a shape-forming process to prevent oxidation of molten metals, can create shapes, in an atmospheric environment, out of titanium, aluminum, and other oxygen-averse materials, without the use of a chamber.
- 3. The monitoring feedback function uses a camera and a sensor to monitor modeling conditions, and, based on analysis results, control laser output and other modeling conditions in real-time, to ensure a stable melting and coagulation of metals. This function automatically optimizes modeling conditions, minimizing the time for trial and error to finalize conditions.
- 4. The AI technology adopted for use in the LAMDA series printers helps them detect problems in processes and prevent equipment malfunctions.
Formnext2022’s official website: https://formnext.mesago.com/frankfurt/en.html