Omron’s Four Ways to Keep Your Workers Safe Around Conveyor Systems
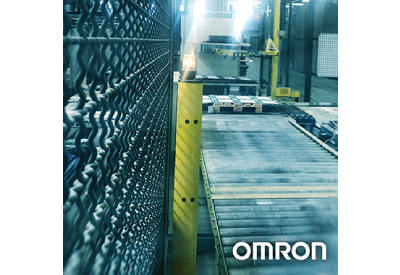
February 25, 2022
Conveyor systems play an important role in industries like packaging, food and commodity, and semiconductor manufacturing, and they vary depending on the type, weight, and dimensions of products being transported, and the environment in which they are installed. One thing that all such systems have in common, however, is a certain set of functional safety requirements. A comprehensive approach to keeping your team safe and your machines running will always start with a risk assessment to identify what risks the workers will be exposed to when performing activities like maintenance and troubleshooting. Omron looks at four converyor-related safety considerations you should be aware of.
1. Be sure to guard all pinch points.
The idea of a pinch point seems self-explanatory, but there are actually several categories of areas that could be pinch points. As detailed in OSHA 1910.211(d)(44), these are places where part of a person’s body could be caught:
- •Between the moving parts of a press or auxiliary equipment,
- •Between moving and stationary parts of a press or auxiliary equipment, or
- •Between the material and moving part (or parts) of the press or auxiliary equipment.
Nip points are a subcategory of pinch points that involve rotating objects like gears, rollers, belt drives and pulleys. Although the choice of guard will depend on the specific characteristics of the machine, it remains necessary that all pinch points must be guarded to keep operators safe.
2. Select the appropriate emergency stop devices.
Since conveyors come in different lengths and layouts, it does not always make sense to use a typical pushbutton emergency stop. This is because workers might not always be close enough to reach the button and stop the system when an emergency occurs.
A cost-effective approach would be to use a rope switch, which offers a range of spans. Rope switch installation is simple and can be done all along the conveyor’s perimeter. This means that a person working at any point of the conveyor will have easy access to the safety device and will be able pull the cord to stop the system if necessary.
3. Design a working safety circuit.
All safety input devices, including E-stop pushbuttons and rope switches, must be connected to safety-rated logic devices (either safety monitoring relays or a safety controller). Non-safety-rated devices are insufficient for this purpose and should not be used.
Built-in self-monitoring capabilities and redundant circuits are important for ensuring that the safety function prevails in the case of a component failure like a short circuit. The system should also automatically test the correct opening and closing of the safety devices in each on-off cycle.
4. Make sure your operators are well trained on safety.
Once you have implemented a safety solution, and it has been validated and verified, the next step is training. You will need to train workers on the important conveyor rules, including general operation and maintenance. You should also consider training on functional safety to make sure that everyone understands how safety devices work and how they should be maintained.
Since many conveyor-related injuries occur when workers are performing maintenance activities, putting clear lockout/tagout policies in place and training them on the use of lockout devices to isolate energy sources for machinery to prevent accidental activation is key.
Want to learn more about our safety services? Click here