Mecademic Robotics Releases New Firmware for its Meca500 Robot
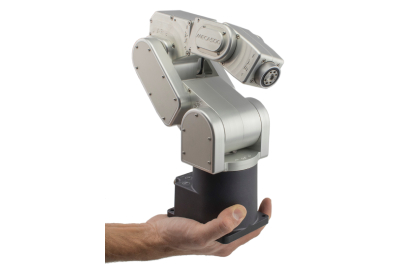
February 7, 2022
Mecademic is pleased to release firmware version 8.4 for its Meca500 industrial robotic arm. Mecademic’s firmware releases are provided free of charge, along with complimentary technical support.
Features & benefits
- •Joint 6 multi-rotation with cartesian moves
Although rotating Joint 6 beyond the ±180° has always been possible with the Meca500 R3, it was limited to Joint-move-commands. With this new firmware, both point-to-point and linear commands can now be used outside of this limit. Apart from the benefit of no longer being limited in Cartesian space and requiring switching to Joint commands, new applications are now easier to implement directly with the Meca500. It’s now easier to use the Meca500 for dispensing, capping, testing, and any other application that requires moving Joint 6 beyond the previous default limits. Of course, we have now introduced a new configuration parameter, to specify the desired turn for joint 6. By default, the automatic configuration for this turn parameter is disabled, please read the programming manual before enabling it.
- •User-defined joint limits
Users can now redefine the software limits of individual joints. The robot will not be able to move outside these limits. It will also generate an error if it starts from a position outside of the specified limits. This feature can help to define a safe robot workspace for your applications. Cartesian range limits are still in development and will be released as part of a future firmware release.
- •User-defined torque limits (sensitivity)
It is now possible to lower the torque limits of individual joints. This is set as a percentage of the maximum possible torque available to each joint. This feature comes with configurable events as per the application’s requirements. This is very useful when working with sensitive components. Although the robot can now be made to stop with light contact, this feature was not designed for collaborative applications.
- •Real-time monitoring data
Although available as a beta feature in previous versions of the firmware, real-time monitoring data is now released as an official feature. Real-time data allows users to stream data in real-time (up to 1ms) over port 10 001 in TCP/IP. The data is also user-configurable (Positions, Torques, Velocities, etc.) Please consult the manual for all available options. This feature enables the user to receive the real-time status of the robot for better monitoring and coordination with other components.
- •Request (Get) commands
Request commands are now available for all Set commands in the robot. This allows users to confirm whether the parameters were successfully set as commanded prior to execution.
Additional information on Meca500 can be found here